The PriestmanGoode design consultancy has been working with Lantal to explore how digital processes can help reduce waste in material manufacture. A key part of the collaboration is Lantal’s Deep Dyed Carpet, an aviation carpet process which won the Sustainable Cabin category of this year’s Crystal Cabin Awards.
Conventional aviation carpets are made using a yarn-dyeing process, which can be slow and energy intensive. If an airline wants to specify a complex and colourful carpet pattern, that can increase weight and cost, and add risk in meeting all airworthiness requirements. Lantal’s Deep Dyed Carpet uses a digital technology that enables design freedom and customisation while minimising weight – and which uses a water, CO2 and waste-efficient production process.
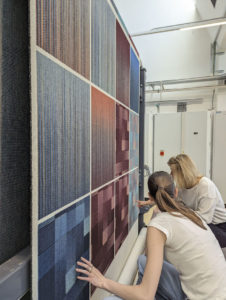
Lantal claims that, compared with a conventional aviation carpet manufacturing process, CO2 emissions are reduced by 40%, water consumption by 60%, waste by 80%, and carpet weight by 25% (compared to conventional two-frame carpets).
The process is also time efficient, with samples and orders able to be delivered to clients in days rather than several weeks, and with reduced minimum order quantities. Only the required dimensions are produced for each carpet order, in a methodology comparable to that of 3D printing, or the zero-waste pattern cutting widely adopted in the fashion industry.
The statistics and design possibilities caught the attention of the team at PriestmanGoode, who have created three designs using Deep Dyed Carpet, each looking forward while respecting traditional craft.
The studio explored the Lantal archive to get a feel for the company, its traditions and its products – quite a task as the Swiss company has been in the carpet business since 1886, and in aviation carpeting since 1954. PriestmanGoode then looked at what the next step could be for carpeting, considering factors such as how colours can contribute towards well-being, and how printed patterns can facilitate wayfinding and accessibility.
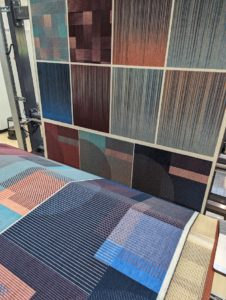
A collection of three designs, in three colour ways and therefore nine options, was then created. The designs comprise the bold Maximalist Energy scheme, the Nostalgic Heritage scheme, and the calming Earthscape colour scheme. You can see from the images that the designs include overlapping and interlacing geometries, from circles to stripes, squares to diamonds, some gently blended, some more sharply defined. It is clear to see the potential for incorporating those wayfinding and accessibility factors into an aesthetically pleasing design.
If you like what you see, the nine design options are now commercially available, with fully bespoke solutions also available, thanks to Lantal’s flexible digital technology.
“Change, towards a more sustainable future, will only occur through collaborative practice across design and manufacture,” said Maria Kafel-Bentkowska, head of colour, material and finish (CMF) at PriestmanGoode. “In a traditional sampling process for aviation clients, a minimum production of 5 metres of carpet is necessary in order to present a single sample. The new process reduces waste in production dramatically, but no aspect of the traditional process is compromised in any way.”
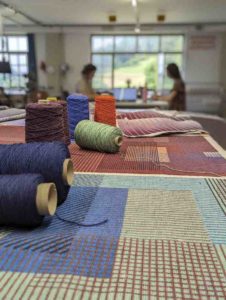
She added that reductive processes such as those used in the manufacture of Deep Dyed Carpet are important aspects of PriestmanGoode’s ‘Route to Zero’ approach to more sustainable design in aviation and other transport sectors. “In a live project, development time is rarely available and therefore we have appreciated the invitation from Lantal to collaborate on this project and for their total freedom in the brief.”