J&C Aero, an aviation design and production company based in Vilnius, Lithuania, has announced that it is investing up to €1.5 million in the acquisition and integration of new high-tech equipment for its aircraft cabin interior production processes. The modernisation programme is aimed at achieving further automation and robotisation of the company’s certified in-house production processes.
The investments include a high-speed CNC vertical mill expected to deliver a three-fold increase in the production of metal items; a digital cutting system to improve the precision of fabric and leather cutting and significantly speed-up the process; a programmable electronic pattern sewing machine for enhanced-quality seams; a fully fledged foam-moulding line for automated production of cushions; and a high-performance spray booth to streamline the painting process.
In addition to the automatisation of production processes, the new equipment will also enable J&C Aero to significantly lower its environmental impact, thanks to a reduction in waste materials, fewer product defects, and more efficient use of raw materials and energy during production.
“The pandemic and the war brought a handful of challenges to the aviation market. The past few years emphasised (yet again) that the cost of being inefficient can be dreadful, both for large and small businesses,” stated Vitalijus Malyška, COO at J&C Aero. “We have been upgrading our infrastructure for several years, and with a new HQ and production facilities just around the corner, it’s time for a new step towards Industry 4.0. The new equipment will enable us to be more precise, more productive and more agile, while also becoming more sustainable as a business.”
According to Malyška, the automatisation and digitalisation program will “significantly improve” the production and maintenance of laminated seat covers, moveable class dividers, windscreens and partitions, and a variety of other cabin interior elements.
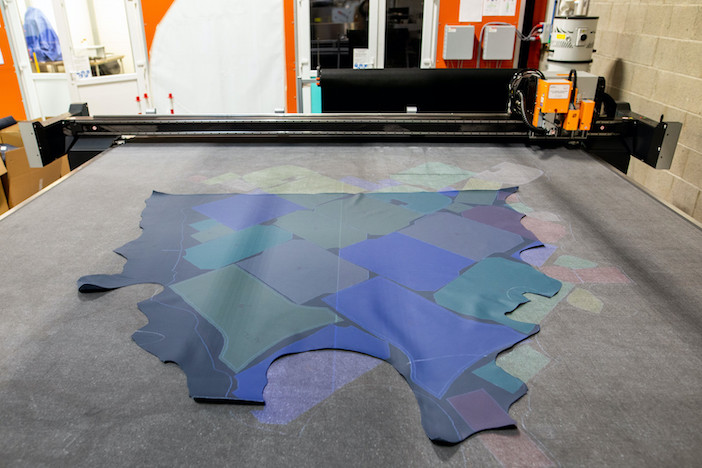