Airbus is progressing towards serial production of the A321XLR long-haul single-aisle aircraft ahead of its planned entry-into-service at the end of summer 2024. The latest step towards the introduction of the aircraft is the inauguration of hangar 246 at the Airbus site in Hamburg, a former A380 hangar with a 24,000 square metre production area.
The 300 staff in the hangar will work with colleagues at hangar 260 (pilot line) and hangar 259 (equipment assembly – which opened last year), forming the infrastructure for serial production of the A321XLR at the site. In short, hangar 246 is the final piece in the industrial set-up for A321XLR production in Hamburg – from structural assembly. to equipment installation and final assembly.
What happens in hangar 246?
XLR stands for ‘Xtra Long Range’, and key to this long-range flight capability is the high-capacity rear centre fuel tank, which is part of the structure of the rear fuselage, located in section 15 and 17 behind the main landing gear bay. These sections are assembled using shells and joined with section 18/19 (delivered by Stelia Aerospace) to form the rear fuselage of the A321XLR. The rear centre tank holds up to 13,100 litres of fuel, which is more fuel than several Additional Centre Tanks (ACTs) combined could previously hold in the A321 aircraft Family.
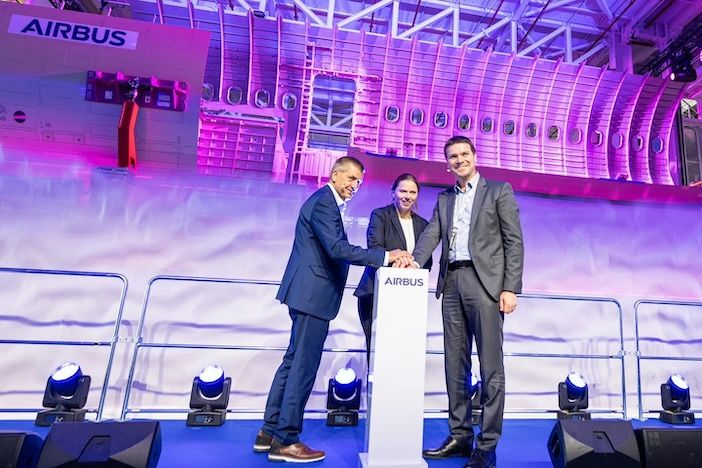
Ergonomics, health and safety
As one would expect of an airframe manufacturer, Airbus has applied great precision in the planning of hangar 246. State-of-the-art tools, and laser- and sensor-controlled measurement systems were used in the planning of the hangar, with key considerations being utility, ergonomics and energy efficiency.
Workers will benefit from the noise containment elements installed, as well as the lifting platforms at working stations, which enable staff to avoid climbing steep stairs and gain optimised ergonomic access to the aircraft sections. The floor grid has been assembled vertically instead of horizontally so that workers do not have to operate in uncomfortable positions such as kneeling. The work stations have also been designed to open up more space for workers to move easily around the working platforms. The energy efficiency measures include large photovoltaic panels installed on the exterior of the hangar.
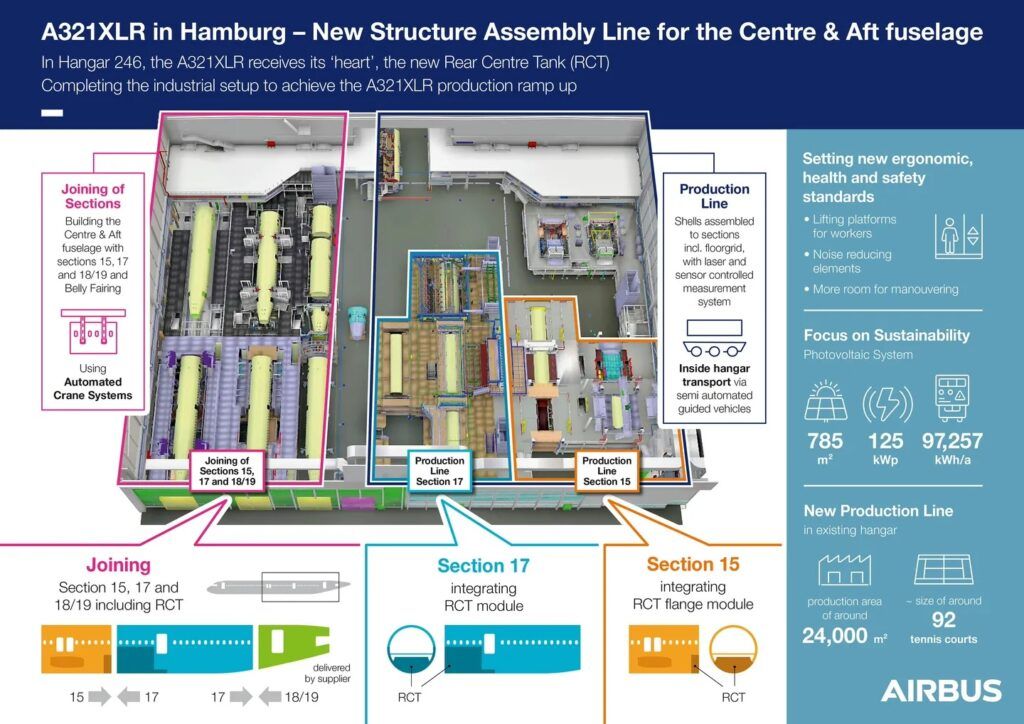
André Walter, head of commercial aircraft production in Germany and CEO of Airbus Aerostructures, said at the inauguration ceremony for the hangar: “Great company, great colleagues, a great moment.” He stated that the start of the new structure assembly was the last brick needed to finalise the industrial setup for the A321XLR in Hamburg, including the many other Airbus plants that play a role in creating the aircraft.
Production of the A321XLR is already running at full speed in Hamburg, and Airbus says the new structure assembly in hangar 246 will make a “fundamental contribution” to achieving target production rates.
Gary O’Donnell, head of the A321XLR programme, said of the hangar: “Our industrial system is one of the most complex and dynamic in the world. The high level of technology, precision and enormous knowledge in interaction with the many suppliers is absolutely unique. What we see here is the result of the incredible knowledge of our people.”