Looking to enhance seated comfort for passengers without replacing seats across a fleet? The latest advances in set comfort technology may hold the answer…
Comfort Design Service
Aerofoam Industries has launched its Comfort Design Service, which is available directly to airlines, designers and seating OEMs that are looking to achieve maximum passenger comfort.
In the case of a new seat platform, the process starts with an expert evaluation of the actual seating structure, either at Aerofoam’s headquarters in California, remotely out in the field or electronically through modelling. The seat structure is then reviewed, as well as its built-in ergonomics and movements if applicable, while taking in all required dimensions. The next step is to produce the first set of trial cushions using foam materials and to begin the on-seat evaluation using a proven process.
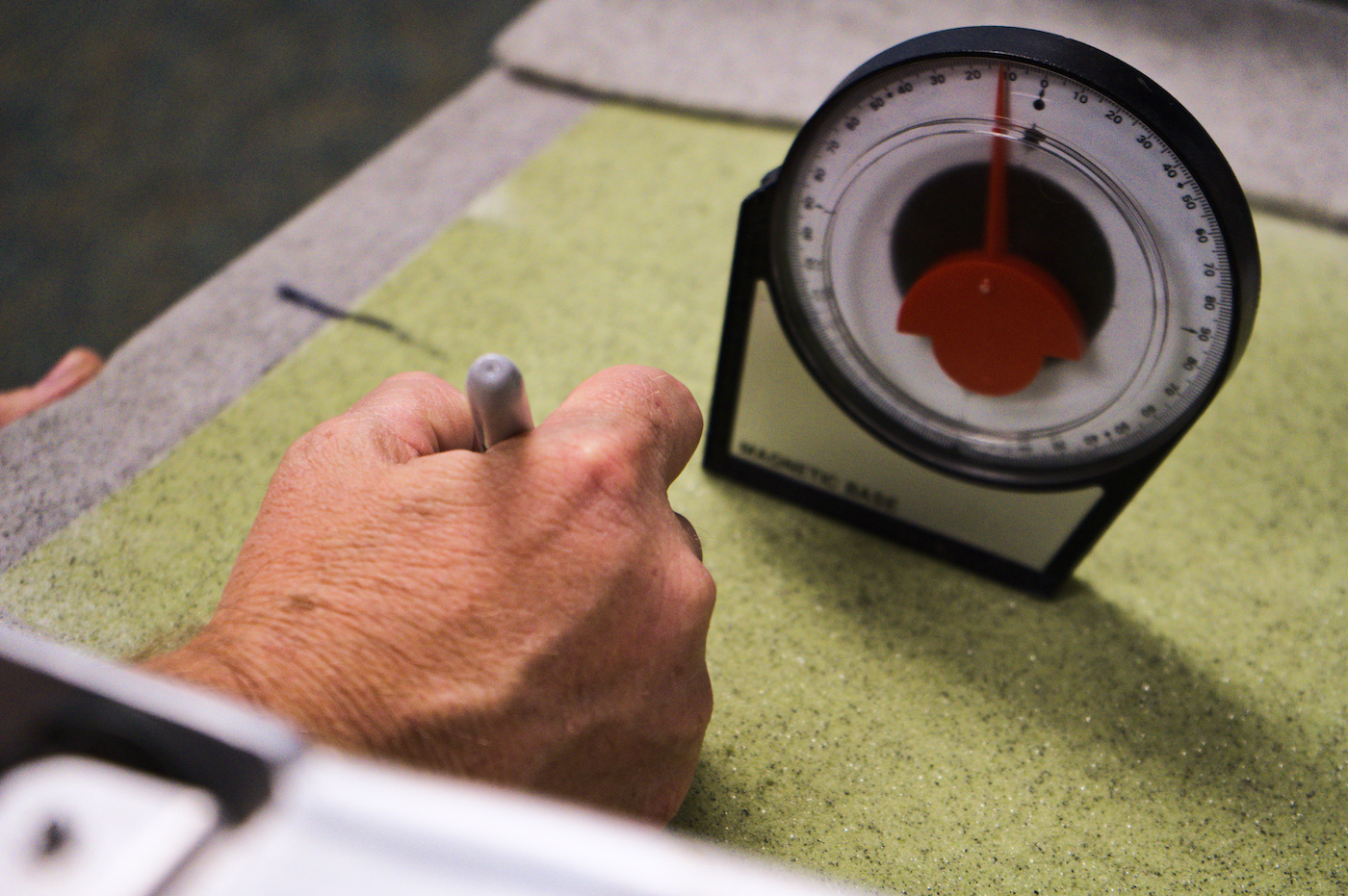
With an existing or in-service seat the process begins with the evaluation of the current cushions and dress covers, and the team then quickly determines what can be done to achieve maximum passenger comfort. These calculated comfort gains are then validated through a series of human factor checks.
Suspension system
Franklin Products, a provider of bespoke upholstery and comfort solutions for passenger seating, has revealed the pre-tension portion of its SLIM diaphragm attachment system, designed to offer passenger comfort, space-savings and weight reduction. This pre-tensioned suspension system is available to both their OEM and aftermarket customers, and is claimed by Franklin to “significantly simplify” the installation and maintenance of an otherwise cumbersome comfort option.
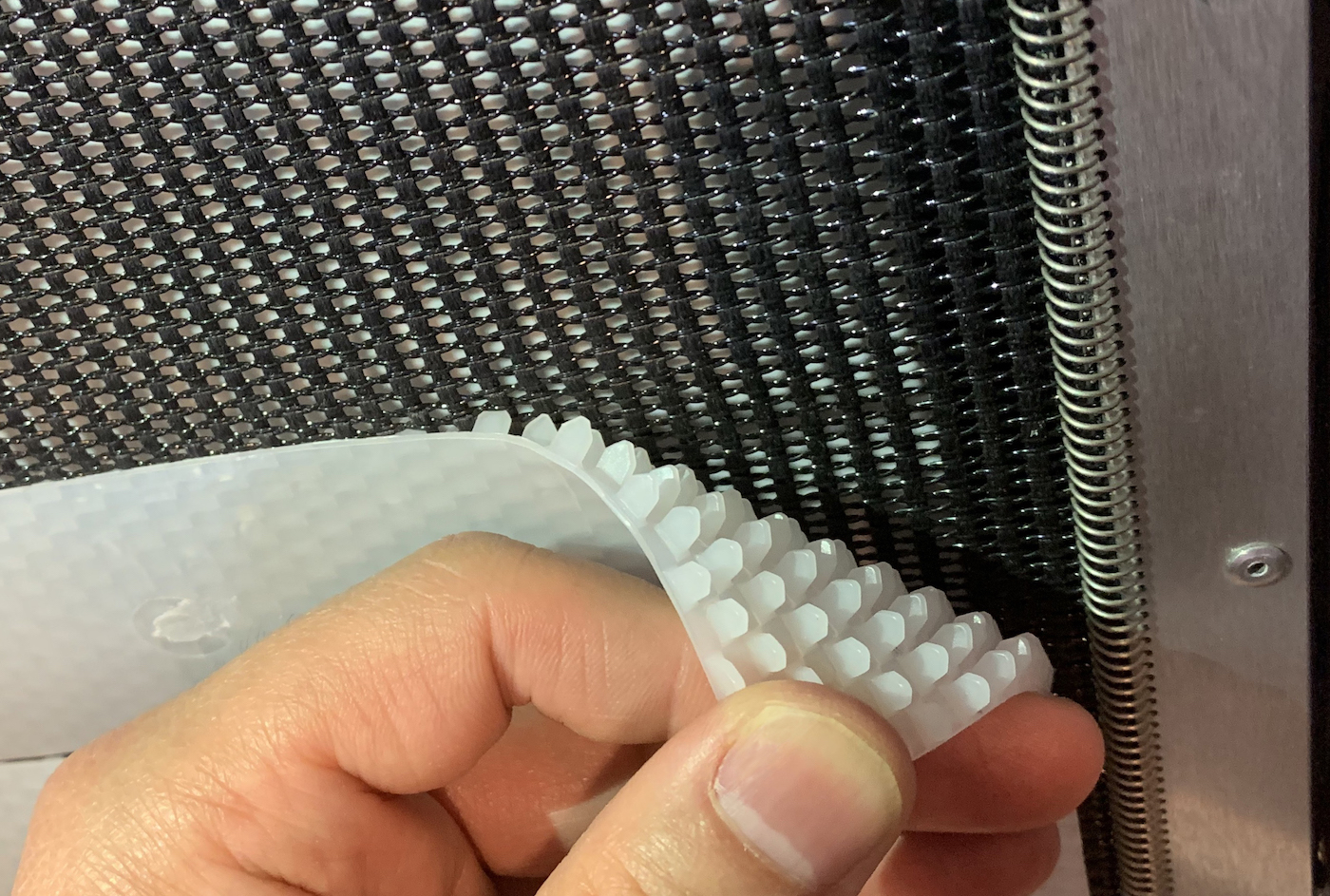
Hybrid seat shroud
Nordam is introducing N-Shroud, a premium-class seat shroud solution. The design was created to demonstrate the company’s proficiency with many types of composites, including prepregs, aluminium, compression-moulded carbon fibre and thermoplastics. By creating new options within the seat supply chain to benefit operators and OEMs, N-Shroud is an exploration of the multitude of materials and techniques available for efficient shroud production.
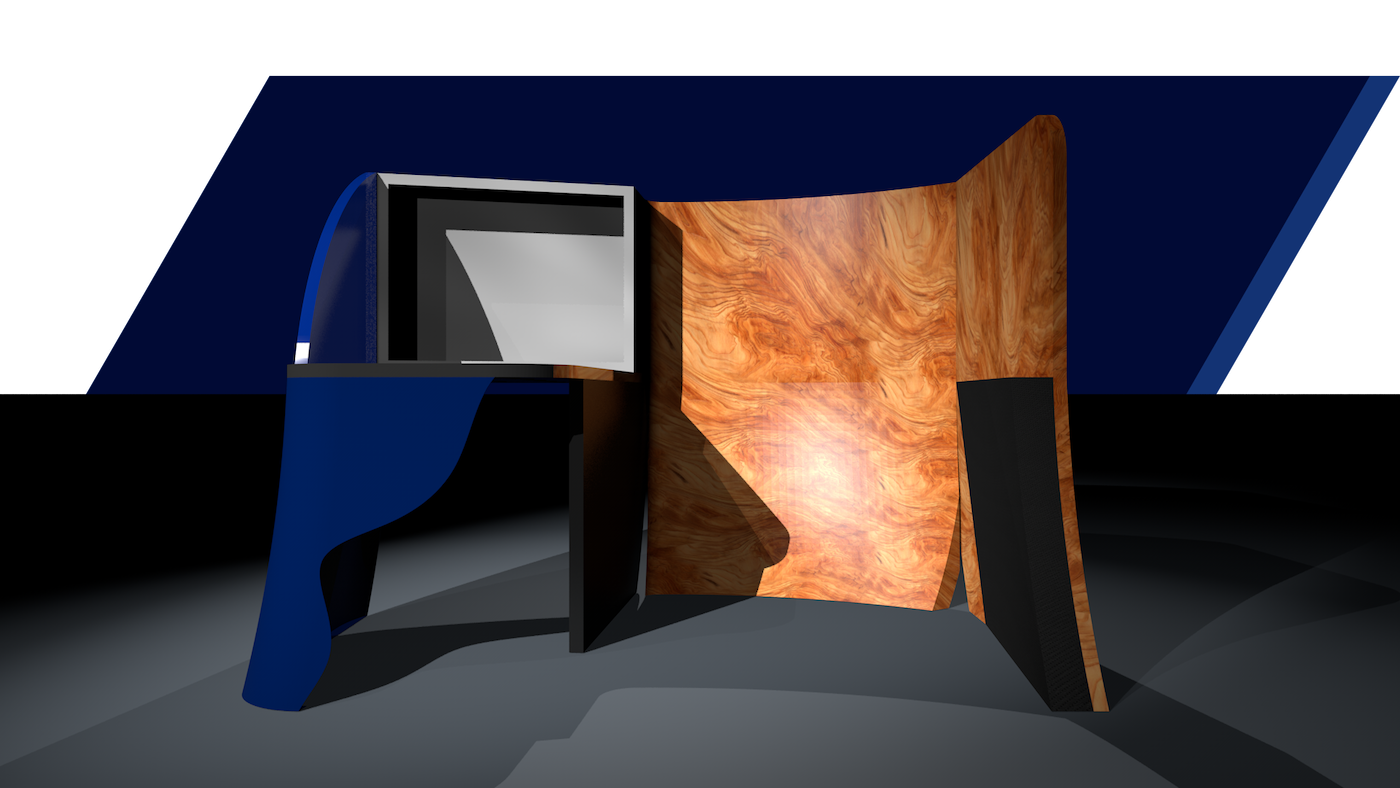
Feel like an El Al pilot
Israel’s national airline, El Al, has partnered with Vanema to implement sleep technologies for pilots on board one of its flagship B777s. The choice of Vanema’s Octaspring foam spring technology follows El Al’s developmental team conducting several internal tests of Octaspring and monitoring how it could help pilot rest and efficiency.
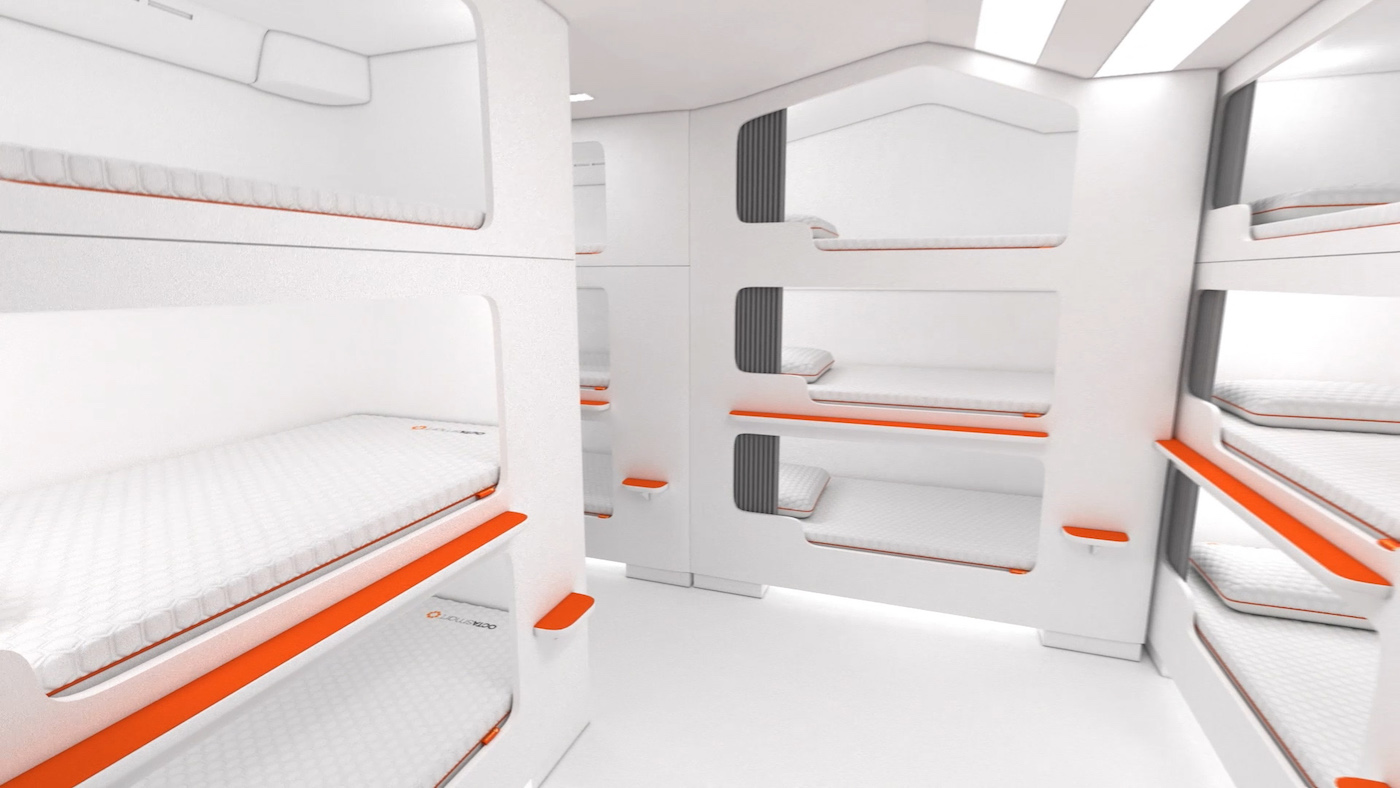
Octaspring provides individual support and is highly breathable, allowing natural thermoregulation as well as higher comfort levels. Octaspring technology is also claimed to uses 50% less material in its production than some other mattresses, saving up to 3kg of weight per mattress.
El Al plans to continue monitoring crew feedback before rolling out Octaspring across its entire fleet of B777s.
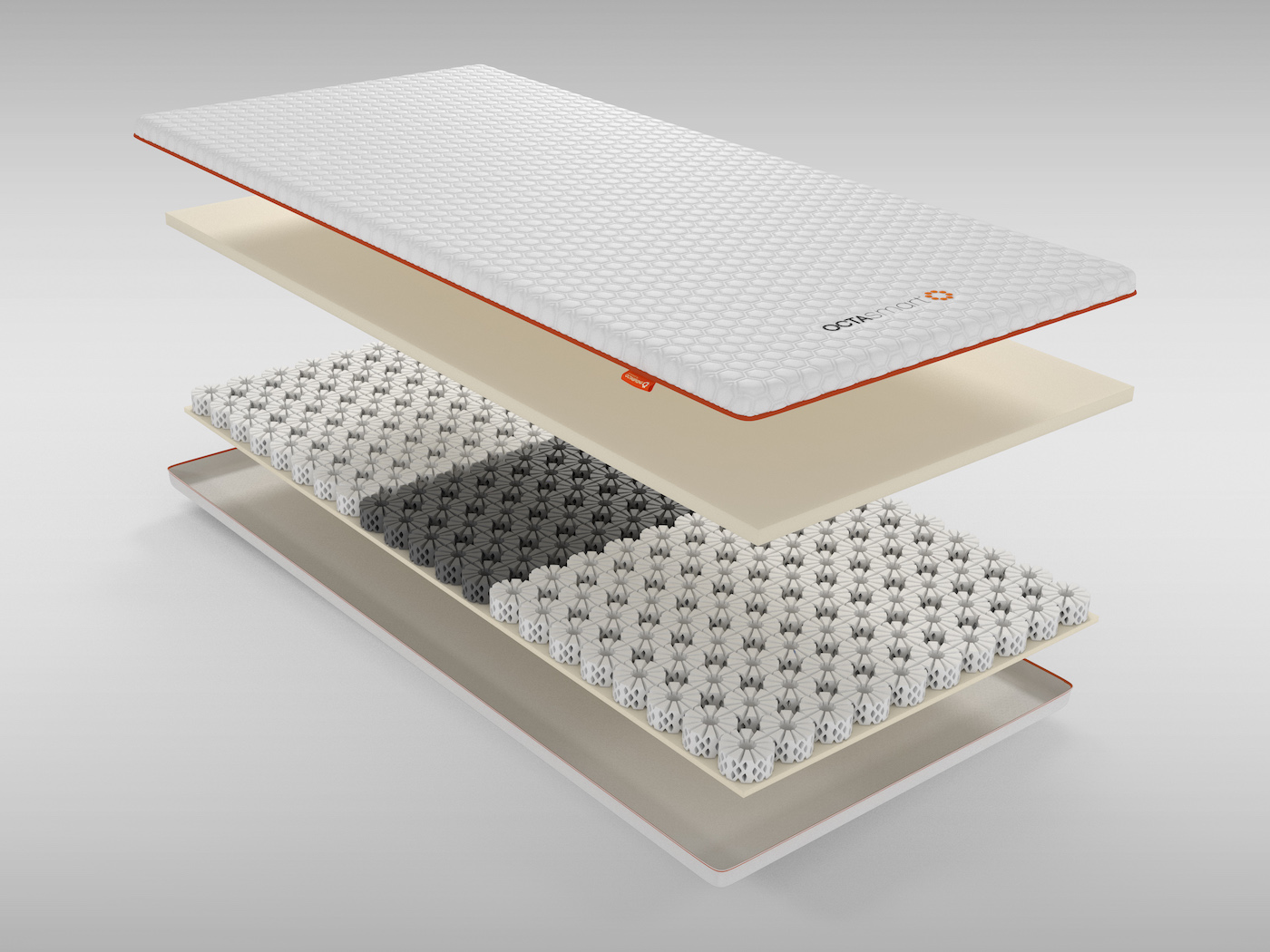
Octaspring won a 2017 Crystal Cabin Award for Best New Material Innovation and is now available in a fully certified product portfolio of aircraft seats and cabin crew mattresses.
Extra-rigid foam
Cellular materials technology expert, Zotefoams, has developed a new closed-cell OSU grade foam – Zotek F OSU XR – to extend its High-Performance Product (HPP) line.
This latest polyvinylidene fluoride (PVDF) foam is an extra-rigid closed-cell crosslinked foam available in densities of 120 and 150kg/m3. Complementing the flexible, semi-rigid and rigid grades already available in the Zotek F OSU range, the introduction of XR extends Zotefoams’ scope of application in aircraft interiors. Zotek F is already used by aircraft manufacturers for window seals, soft-touch trim, close-outs, insulation, carpet underlay and environmental control systems due to its light weight, ease of processing and its frequent suitability to replace composite materials.

“With the introduction of the XR grade, we are extending the weight-saving benefits of the Zotek F OSU range to locations such as the interior of seat pods, stowage lockers, rigid armrests and tray tables, while reducing weight by as much as 70% on a like-for-like basis,” says James Bridges, director of high-performance products at Zotefoams.
Grades of Zotek F can be laminated together to create a single material that is rigid on one side and soft/flexible on the other, and can be formed into curves and complex shapes. The potential weight savings achievable by replacing solid thermoplastic and silicon components with Zotek F are also attractive.
Zotek F features in this year’s Crystal Cabin Awards as part of the submission by MGR Foamtex. Its MGRSoftWall NextGen ‘soft touch’ cabin panels feature dual-density foam from Zotefoams that is claimed to reduce weight by up to 60%, translating to claimed savings of up to 100kg per aircraft.