The aerospace plastics market is set to grow from its current market value of more than US$45 million to over $75 million by 2025. Ongoing modernisation programs for existing aircraft fleet to enhance airplane design and materials used for construction, coupled with an upsurge in aircraft deliveries across the globe will propel the aerospace plastics market penetration over the forecast period of 2018-2025. Growing demand for lightweight, next-generation and fuel-efficient aircraft are significantly increasing the adoption of plastics for multiple aerospace applications. The contribution of plastics to reducing aircraft weight contributes significantly towards improving efficiency and lowering emissions.
The increasing usage of plastics in aerospace components can also be attributed to the benefits offered, including superior protection from ultraviolet radiation, moisture and elevated temperature. Additionally, advanced engineered plastics such as Polyetherketoneketone (PEEK) offer a wide range of features including thermal stability, flame retardancy and chemical resistance, thereby boosting the market share. However, aircraft components manufactured with plastic are hard to examine for flaws, resulting in quality variations, thereby hampering the market size of aerospace plastics.
The inclusion of polymers with the ability to withstand higher temperatures and impart excellent corrosion resistance will propel the aerospace plastics market share. Industrial thermoplastics including Acrylonitrile Butadiene Styrene (ABS) are extensively used to manufacture storage bins for cabin interiors. The thermoplastics provide higher durability and meet flame and smoke requirements for air carriers. Moreover, the plastics enable manufacturers to enhance aesthetic appeal and the passenger experience.
Growing development of high-temperature engineering polymers such as polyethylene sulphide and polyetherketoneketone (PEKK) to provide alternative for aluminium components will escalate the aerospace plastics market size. The polymers have high stiffness, impact resistance, tensile and compressive strength. Superior chemical properties such as excellent combustion resistance, flame retardance and low-level smoke generation is increasing product demand. Further, development of new grade high strength and low weight materials such as HT-23 will drive the industry growth.
Stringent regulatory norms are mandating the reduction of carbon emissions from aircraft and improving efficiency, thereby encouraging aerospace participants to significantly increase the usage of plastics.
Aerospace plastics market
The superior design flexibility and higher degree of freedom are some of the major benefits offered by the plastics that are significantly boosting the aerospace plastics market share. Moreover, the higher modulus of elasticity along with lower material weight compared to other metals including steel and aluminium make it ideal for designing multiple aerospace components, thereby escalating the industry share.
Advancements in manufacturing technologies along with the proliferation of 3D printing techniques are providing a positive outlook for the aerospace plastics market expansion. The 3D printing of parts enables for fewer tooling changes, reduced production time, and improves efficiency significantly. Aircraft manufacturers are continuously investing in 3D printing technologies for manufacturing their aircraft. For instance, in 2015, Boeing filed a patent associated with the 3D printing of replacement aircraft parts.
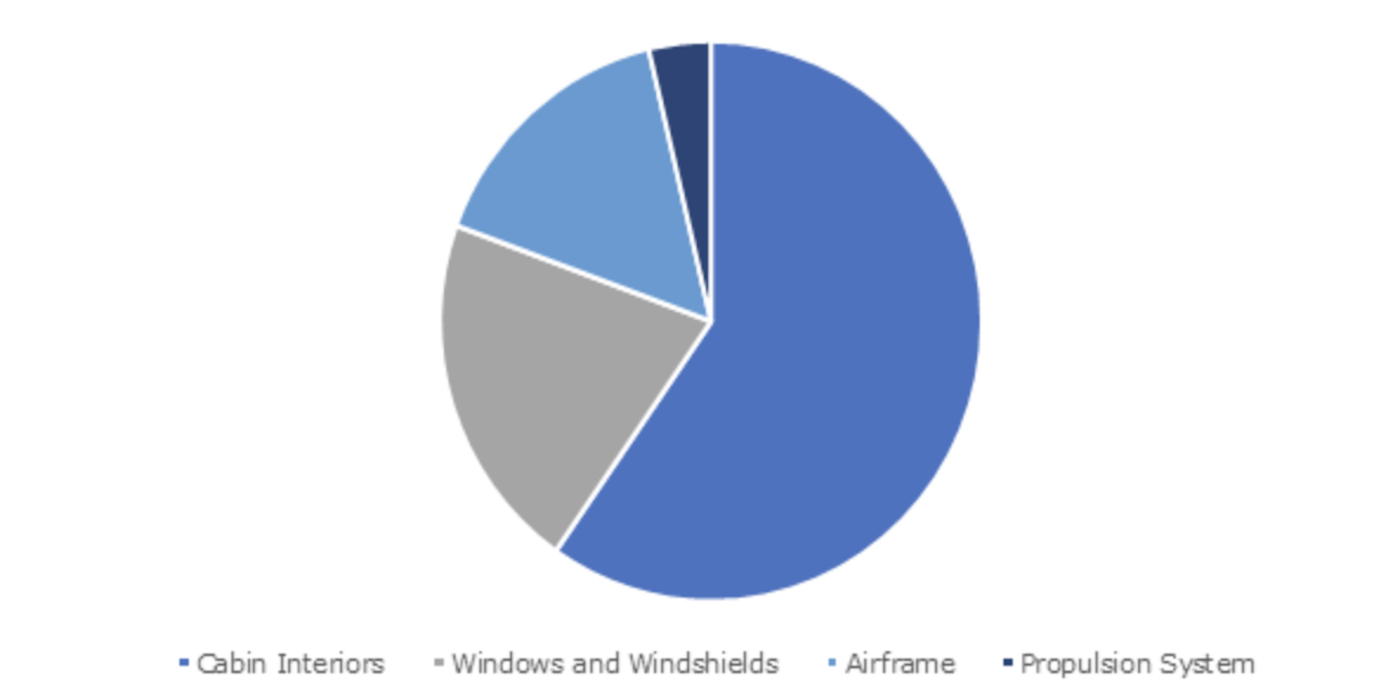
Industry participants are focusing on manufacturing aircraft parts that meet the stringent smoke, toxicity, and flame requirements, as set by multiple regulatory bodies including the Federal Aviation Administration (FAA). Additionally, advancements in plastic technologies that enhance the limits of torque handling, gear drive, and load-bearing capabilities in the aerospace sector are further expanding the aerospace plastics market penetration over the projected timeframe.
Military aircraft will showcase a considerable growth in the aerospace plastics market owing to rising defence expenditure and increasing security concerns across the globe. Higher adoption of plastic in military aircraft can be credited to its requirement to offer effective insulation from radar. Moreover, the provision for zero conductivity along with the significant weight reductions are positively influencing the segment growth. Moreover, the US Department of Defense is continuously developing aerospace plastics materials for improving horizontal and vertical agility of aircraft during combat missions.
US aerospace plastics market, by aircraft, 2018 & 2025, (US$ thousand)
Commercial aircraft lead the aerospace plastics market, with vast fleet sizes to accommodate passengers. The aviation industry participants are implementing high-performance polymers with sliding properties for dry operations under extreme conditions. The air carriers utilize multiple thermoplastic grades, including POM-C, POM-H, PA66 and PTFE in aircraft components. These components have high resilience, electrical insulation and good machining properties.
The cabin interior segment holds significant revenue share in the aerospace plastics market owing to the development of lightweight foam material that enables aircraft component manufacturers to reduce the overall parts weight. For instance, in September 2018, BASF developed polyethersulfone (PESU) foam that is suitable for manufacturing complex-shaped components in aircraft cabin interiors. Further, development of fire rated thermoplastics such as Royalite for cabin interiors products will escalate the segment penetration over the study timeframe.
Windows and windshields accounted for a considerable share of the aerospace plastics market size owing to the prevention of glass layers shattering in windows, with the utilization of durable and chemical-resistant plastic. Additionally, the windshields also offer reduced reflectivity and regulate light and heat transmission flow to the interiors, thereby supporting the segment expansion. Rising MRO activities along with the replacement of ageing components with advanced plastics are expected to boost the segment size.
Line-fit orders will account for the majority revenue share in the aerospace plastics market share over the study timeframe. Increasing aircraft production rates across the globe are positively influencing the segment share. Moreover, the capability of replacing metal machined aircraft parts with reduced design changes are boosting the segment size. The longer service life, coupled with lower maintenance requirements, are further encouraging aircraft manufacturers to incorporate plastic materials into aircraft.
The retrofit segment will witness significant growth in the aerospace plastics market size owing to continuous refurbishment activities to enhance the customer experience. The airliners are collaborating with the aftermarket service providers for cabin repairs and modification activities. For instance, in November 2018, Satair and Regent Aerospace entered into an agreement for cabin upgrades and refurbishment services that include plastic components, cushions, arm caps and dress covers.
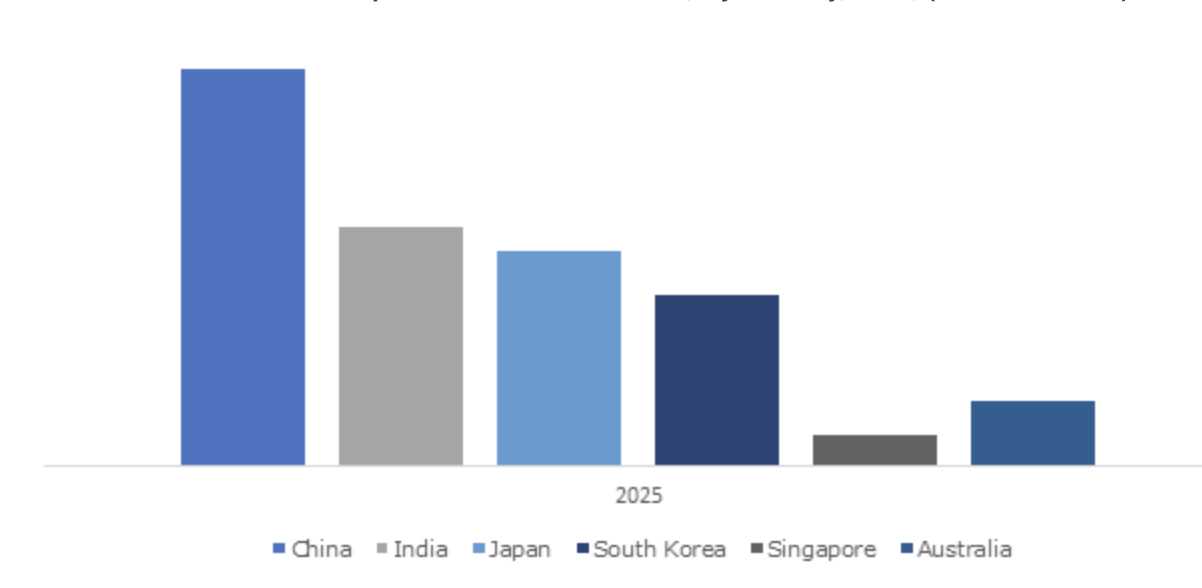
North America will account for the highest volume share in the aerospace plastics market size. The presence of multiple manufacturers focusing on developing fuel-efficient aircraft is further boosting the regional share. Moreover, rising fuel costs along with stringent regulatory norms are further encouraging players to incorporate plastics in their aircraft. Aircraft manufacturers are developing customised plastic manufacturing processes for improving their margins and increasing profitability. For instance, in 2019, Northrop Grumman was granted a patent associated with aerospace composite 3D printing process based on a fused filament fabrication (FFF) technology.
Major players in the aerospace plastics market include Saint Gobain, Ensinger Plastics, SABIC, Victrex, AIP, Drake Plastics, BASF Corporation, Solvay, Mitsubishi Chemical Advanced Materials, Superior Plastics, Polyfluor Plastics BV, Eptam Precision Plastics and Mitsubishi Chemical Advanced Materials. Industry players are engaged in mergers and acquisitions along with newer product launches, with the aim of expanding their market share.
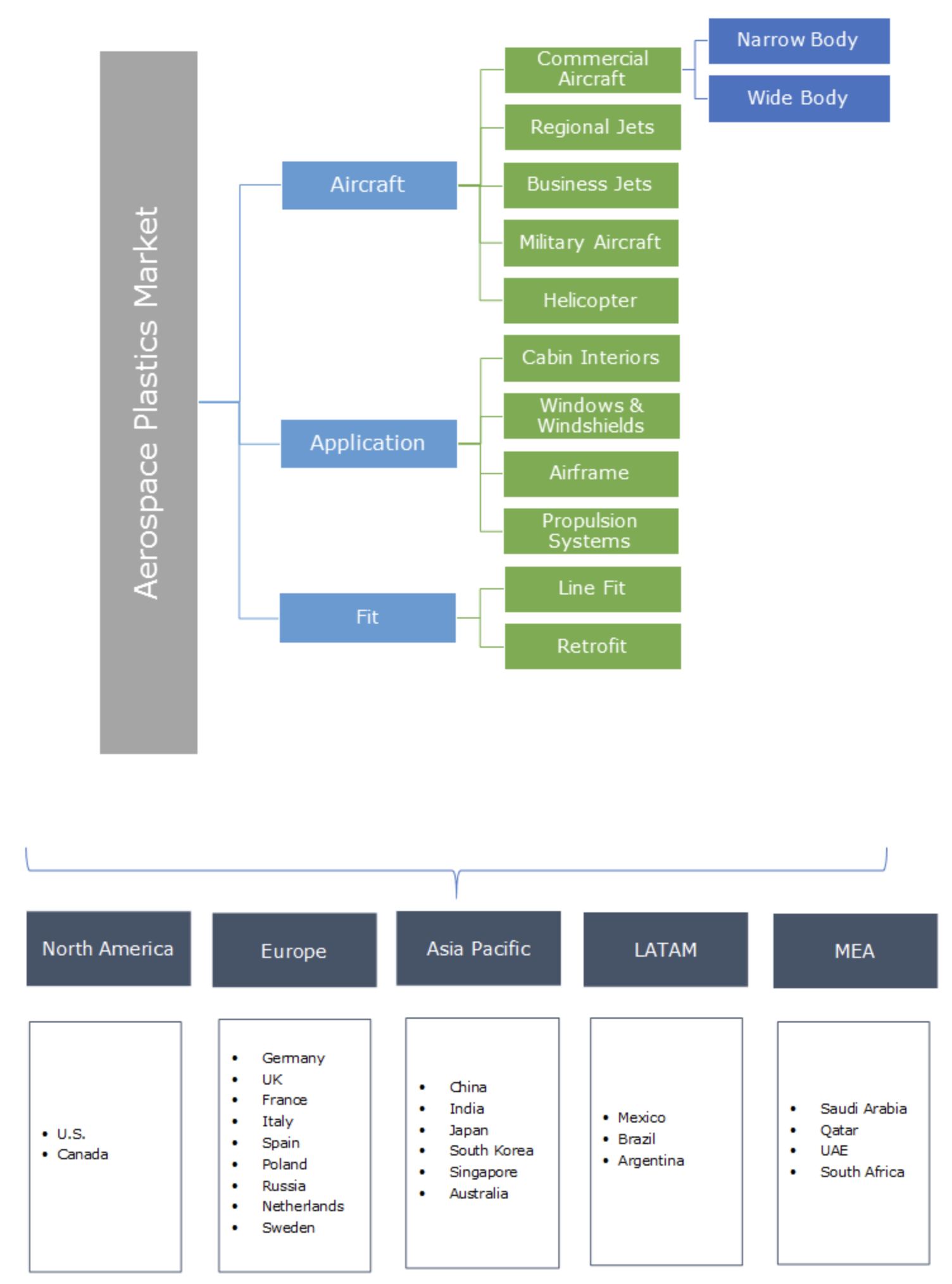