The aerospace industry’s goal to achieve net-zero carbon emissions by 2050 has been a key motivator for manufacturers like STG. As lighting experts, we are a small part of the puzzle, but it’s important for every organisation – big or small – to do its bit in contributing to a greener future. A lot of work has been happening behind the scenes over the last few years, with sustainability at the front of mind of researchers seeking to create innovations.
At Aircraft Interiors Expo (AIX) 2024, STG unveiled the world’s first sustainable emergency floor-path marking system, saf-Tglo Eco E1. This innovative, biodegradable version of the saf-Tglo range is an important step in the evolution towards more eco-friendly aviation product design. The Eco E1 floor-path marking solution not only ensures passenger safety and cabin aesthetics, but also addresses the urgent need for sustainable alternatives compared to what is already on the market.
Tracy Vyas-Middlecoat, STG’s research and development scientist, is the technical lead for Eco E1. She worked with the wider team at the company, as well as a student at University College Dublin, who carried out their master’s thesis with STG.
Tracy explains the detailed process of creating the latest product.
The first step of the process
The first step was to search for a sustainable material for the track, as it makes up the bulk of the product. Polycarbonate is a popular material for use in aircraft interior products, as it is strong, sturdy and long lasting. However, research highlighted that, due to its complex chemical structure, recycling of polycarbonate is complicated.
While chemical recycling has the potential to fully break down polycarbonate, this process is currently mostly at the academic level and is only just entering the commercial market. Mechanical recycling is commercially available, but it can raise issues in traceability – something that is vital for aerospace applications.
We gathered the feasible material options on the market, from post-consumer recycled polycarbonate, to polymers made from bio-oils, and even a sugar-based polycarbonate equivalent, and used these to run manufacturing trials.
It was a process of trial and error, and we had some spectacular failures. For example the sugar-based material, was transparent in raw form, but once melted, turned bright opaque white and jammed inside the extruder like caramel – but at least the smell was nice!
During the extruding process at our supplier, we learned about their in-house recycling system for waste material, which piqued our interest. We investigated mixing 50% of the recycled material with virgin material, which worked surprisingly well. In contrast with some of the other recycled materials that would have to be shipped in from overseas, this is a closed-loop system, which is beneficial from a traceability viewpoint, and also reduces the carbon footprint.
Our aim was to increase sustainability across the full life cycle. We have no control over the end of life of our products. We would love everyone to recycle them, but we know that most consumers will remove them from the aircraft and put them into landfill. We wanted to cover all our bases and use something that would not leave a trace, no matter how it is disposed of.
This is why we have also included a biodegradable additive in the track, which will remain inert whilst the product is in service, but when disposed of, will fully break the polycarbonate down into its base elements, leaving no ‘forever plastics’.
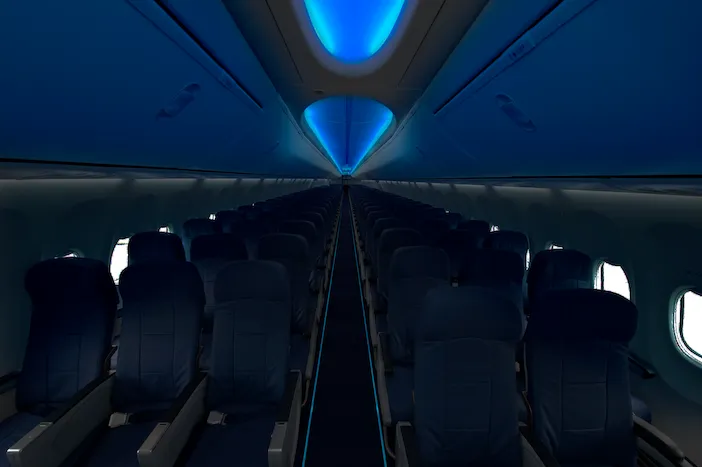
Finding the insert material
Insert material comes in sheet form and is generally made by the mile for commercial purposes, which means it was not feasible to use in any extrusion trials. Luckily we found a UK company that offered sheets made from mechanically recycled materials.
We worked with them to create bespoke sheets which are made from 80% recycled content, are 20% lighter than the sheets used in existing saf-Tglo products, and lead to an assembly that is 80% lighter than legacy STG products. This is a significant improvement to the product, as weight saving is directly correlated to the amount of fuel burnt on an aircraft.
The quest for resin
Finding the right resin was the most challenging part of the process. STG’s PL material is currently held in a solvent-based resin, which introduces VOCs (volatile organic compounds) into the atmosphere. This is detrimental to the environment and can also create an unpleasant odour during the manufacturing process. We wanted to move away from solvent-based resins and investigate water-based options.
This was a difficult task, as these resins are more commonly used for fabric printing because they require a porous surface to bond with. Many trials were required but we ended up with the perfect recipe, using water-based resin and plant-based materials, which meet the same standards as our solvent-based equivalent.
Rigorous testing
Once we had found our materials, we performed fitness for purpose tests. We test flame retardancy, and how well the product deals with exposure to fluids found in and around the cabin. We also test robustness, by rolling a 150 kilogram galley cart over the assembly for 10,000 cycles, which is equivalent to 35 years of service. We conduct this initial round of testing to assess the feasibility of the prototype, ensuring that when we proceed to formal qualification testing, we have complete confidence in the product.
Plans for the future
From start to finish, the process of designing and launching saf-Tglo Eco E1 took a year and a half. We are incredibly proud of this product and of the hard work of everyone involved. saf-Tglo Eco E1 delivers sustainability improvements across the product lifecycle, without compromising passenger safety, reliability, performance or aesthetics. Finding the perfect materials required a considerable amount of trial, error and perseverance.
However, the key takeaways from the project have been invaluable. We gained knowledge in environmentally sensitive design, which has been helpful for future developments. This new approach for Eco E1 also led to two new patents for STG.
The STG team is looking forward to applying this knowledge and new-found materials to the next project, which we look forward to launching very soon.