The aerospace industry is constantly looking for innovative materials that maintain, or even enhance, performance while reducing weight. As with many industries, the focus of these developments often concentrates on the search for sustainable solutions to replace traditional methods and materials. An ongoing collaboration between TRB Lightweight Structures and Composites Evolution is aiming to develop biopanels – using resins derived from sugar cane – as a non-petroleum based alternative to the phenolic panels currently used for aircraft interiors.
Composites have been widely used in the aerospace sector since the early days of aviation, providing lighter weight alternatives to more traditional solid materials. These engineered materials are used extensively throughout the aircraft in both structural and non-structural applications, from flooring and cargo bays to passenger cabin walls, toilet cubicles and partition walls. The mechanical properties of composite panels can be tailored to the intended application, altering the thickness, core construction and skin materials to meet constructor specifications. For example, a Nomex or equivalent honeycomb made of aramid fibre paper coated with a heat-resistant phenolic resin skin is commonly used for non-structural applications, whereas an aluminium honeycomb and epoxy skin provides greater structural integrity and harder-wearing panels for structural panels.
Despite composites having a long history of use in aircraft construction – and an extremely strong track record for safety – the commercial aviation sector is very conservative when it comes to the use of new materials, due to the inherent risks of transporting the general public at over 35,000 feet above the ground. As a result, the industry has extremely stringent specifications and testing requirements for materials and products. The foremost of these is fire, smoke and toxicity (FST) performance, which is a crucial consideration for materials used in aircraft interiors, as these components are most likely to have direct contact with passengers and crew.
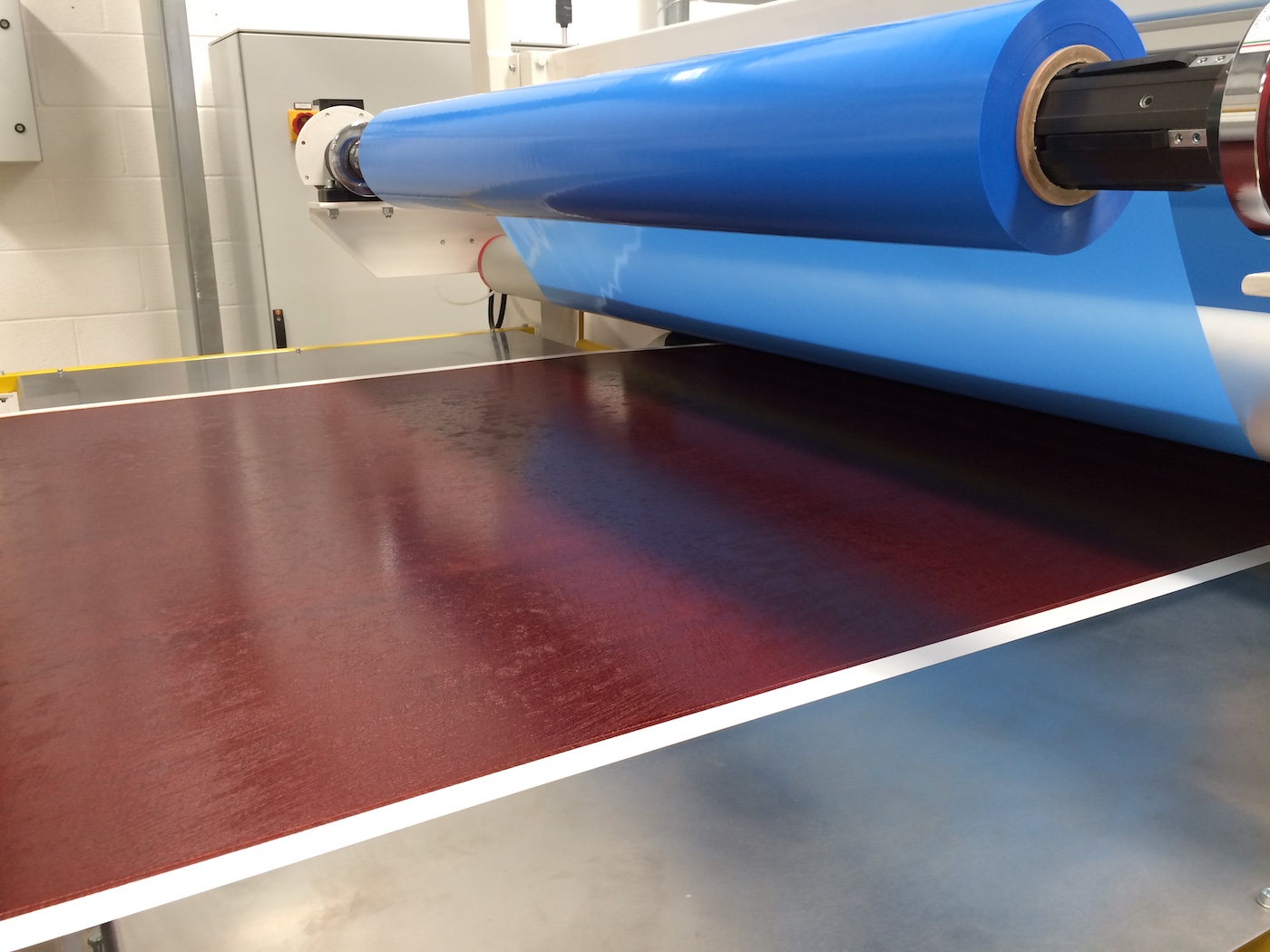
Moving away from phenolics
Phenolic sandwich panels are widely used as a building material – from offices and locker rooms to train and aircraft interiors – as they are easily shaped and moulded, have suitable mechanical properties for non-structural applications, are relatively lightweight, and offer good FST characteristics. Unfortunately the phenolic resins used to manufacture these panels are petroleum-based and toxic before curing, making them more difficult to work with safely. Consequently, there is a growing demand for alterative resins derived from natural sources – making them both more sustainable and less harmful for people and the environment – and a number of bio-based resins are currently under development across various sectors. While phenolic panels are still the standard choice of material for aircraft interior panels, a newly developed resin – polyfurfuryl alcohol (PFA) – is an exciting breakthrough.
PFA is derived from a byproduct of refining sugar cane and has the potential to replace the oil-derived resins currently used for sandwich panel applications. Despite originating from a biological source, the extraction process for PFA ensures a very consistent, high-quality resin that can be produced in large quantities, thanks to the ready availability of biomass waste. It offers very similar mechanical and FST performance to the phenolic resins currently used for aircraft interior panels and, because it does not contain potentially toxic or harmful chemicals, such as free formaldehydes and phenols, it has a lower environmental impact.
Perhaps remarkably, only minimal changes to existing manufacturing process are required to use PFA resins, reducing the outlays and potential barriers commonly associated with the adoption of new materials. Prepreg skins based on PFA are already commercially available (from Composites Evolution), and have been used in the creation of novel sandwich panels (by TRB Lightweight Structures). The main challenge for both phenolic- and PFA-based sandwich panels is the bond strength between the honeycomb core and the prepreg skin.
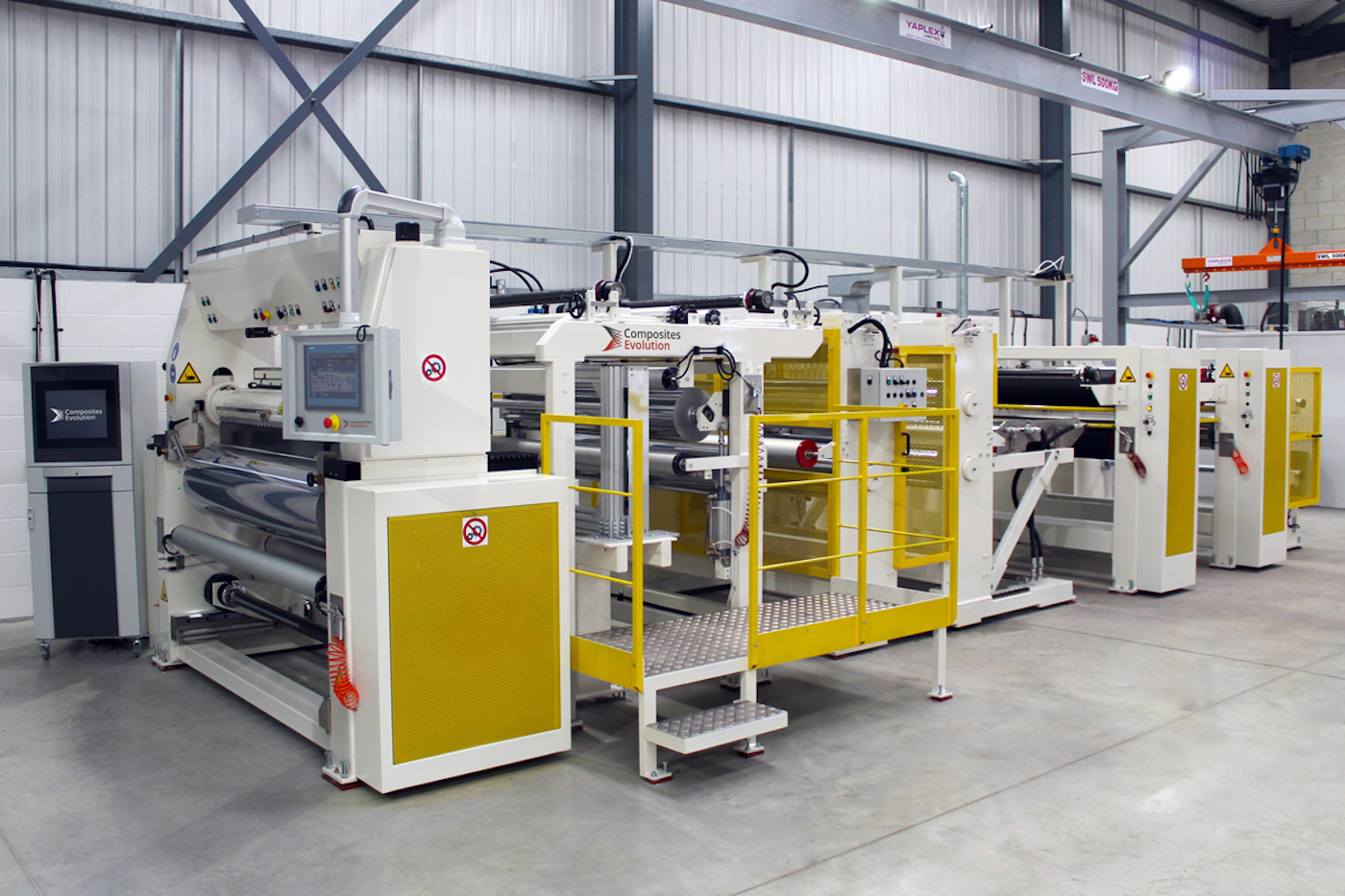
Developing a solution for aerospace
TRB Lightweight Structures and Composites Evolution have collaborated to develop PFA sandwich panels for use in the aerospace sector. In addition to generating the vital FST performance data that is a pre-requisite to adoption, the companies have also looked at further improving the mechanical performance and other characteristics of these biopanels. This work includes testing at elevated temperatures, application of a number of commonly used aerospace finishes – including Tedlar polyvinyl fluoride (PVF) films and both solvent- and water-based paints – and load testing with commonly used insert fittings.
Summary
The aircraft interiors industry is current heavily reliant on oil-derived resins for the construction of widely used lightweight composite panels; however, bio-based resins are now being shown to offer an alternative. PFA is the frontrunner in this area, offering similar mechanical properties and requiring only minor modifications to current construction techniques. Crucially, it offers very similar FST performance to phenolic resins, and is more user- and environmentally-friendly, making PFA biopanels a significant breakthrough in the search for more sustainable materials.