Three Italian companies have joined forces to reimagine commercial aircraft interior design and the passenger experience. The project, named RATIOS, is intended to completely rethink commercial aircraft cabins to meet the needs of various travellers, from those with children to those with disabilities, and also to improve the working conditions of flight attendants and increase comfort for all. The project is comprehensive, with new seat designs, redesigned spaces for overhead stowages, reshaped common areas with fully automated vending machines for food and drink, and touchless lavatories – all constructed using new materials and technological solutions never tested before on aircraft.
The consortium consists of Delta Interior Design (project coordinator), an aircraft cabin design and manufacturing company; Studio Volpi (partner), a company with experience in design concepts, technology and innovation; and Leonardo (topic manager), a global company specialised in aerospace, defence and security, backed with funding from the Clean Sky 2 EU programme.
Economy class cabins are a particular focus for the project, with the team taking into consideration the variety of passenger sizes and that airlines need to make use of all available space in the cabin. They imagine that in future airplanes, the typical alignment of the overhead lockers along the top of the fuselage, would be replaced with a transversal arrangement with a stowage space allocated for each seat. For seats, the cushion could extend, allowing the occupant to stretch their legs with the belts fastened. No more fights to find space for carry-on cases and no more need for contortions in the seat. Regarding materials, the RATIOS team studied composites, and also modern fabrics that are durable and lightweight, fireproof, easily washable, antibacterial and recyclable – and perhaps initially produced from recycled materials.
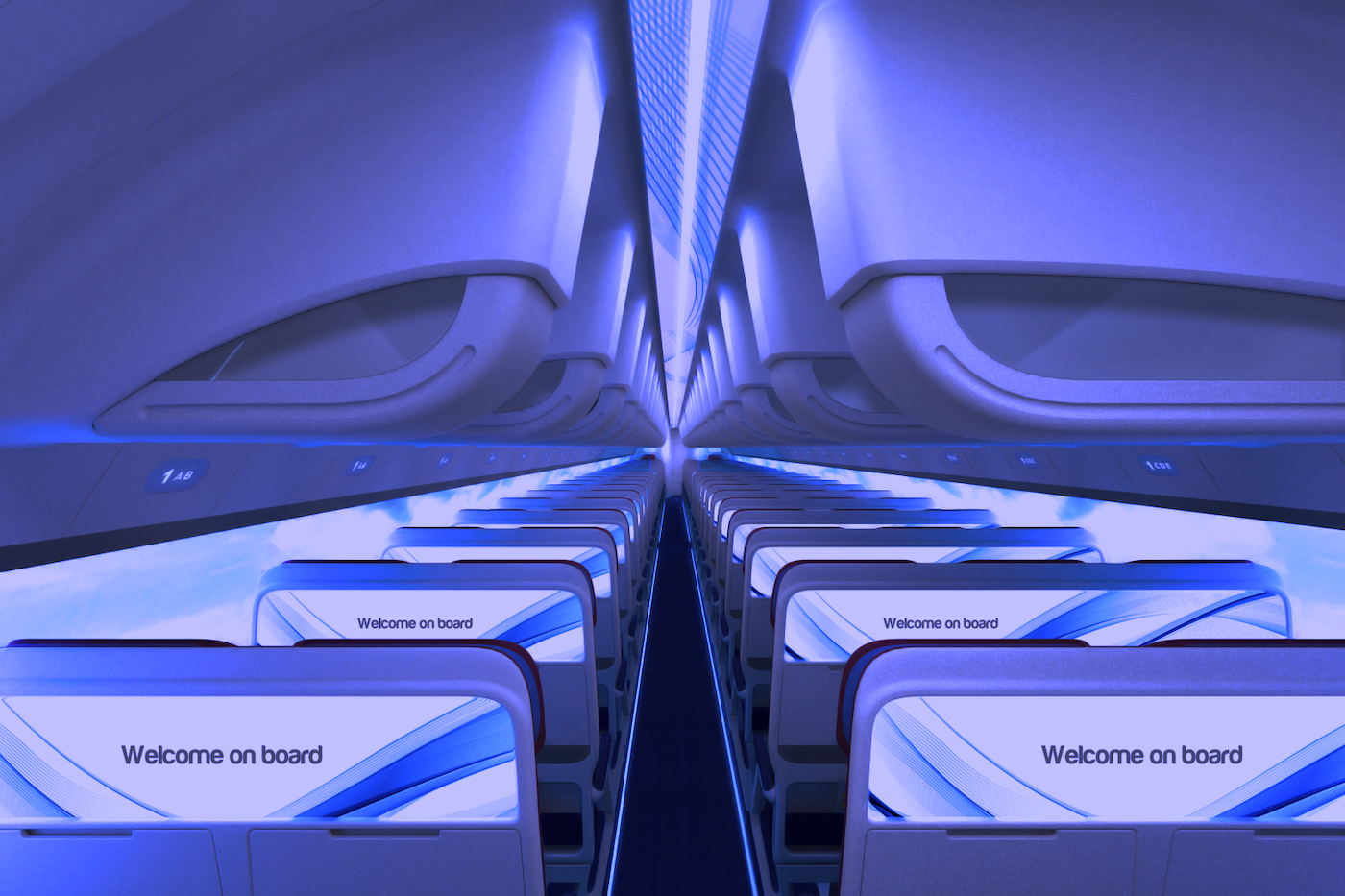
Further ideas for future passenger cabins include a less rigid LOPA, including seats fitted in a club-style orientation, which makes conversations between passengers easier, increases legroom, and is more suitable for child travellers. The windows could be larger and repositioned to give passengers an enchanting view of the the outside.
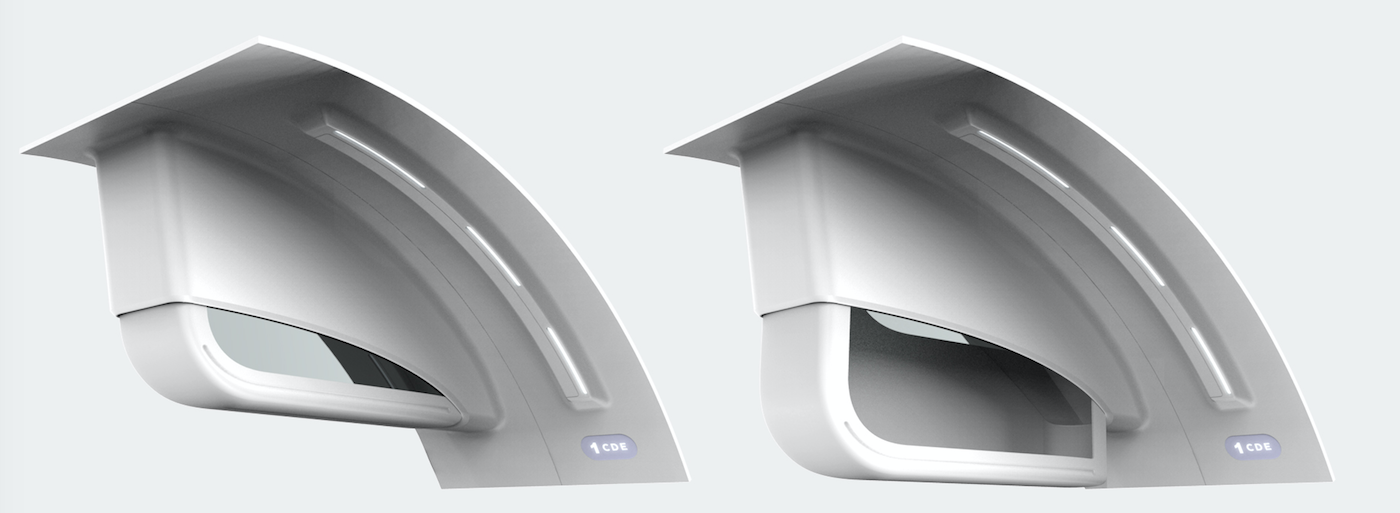
The team has studies several recent cabin design concepts – some improbable, if not impossible – but they believe that very few have any chance of becoming a reality. The companies involved in RATIOS set out to maintain feasibility of design, with a focus on constructive solutions, and certification capabilities. The three companies believe that by bringing together their skills and experience, they can bring their vision to life.
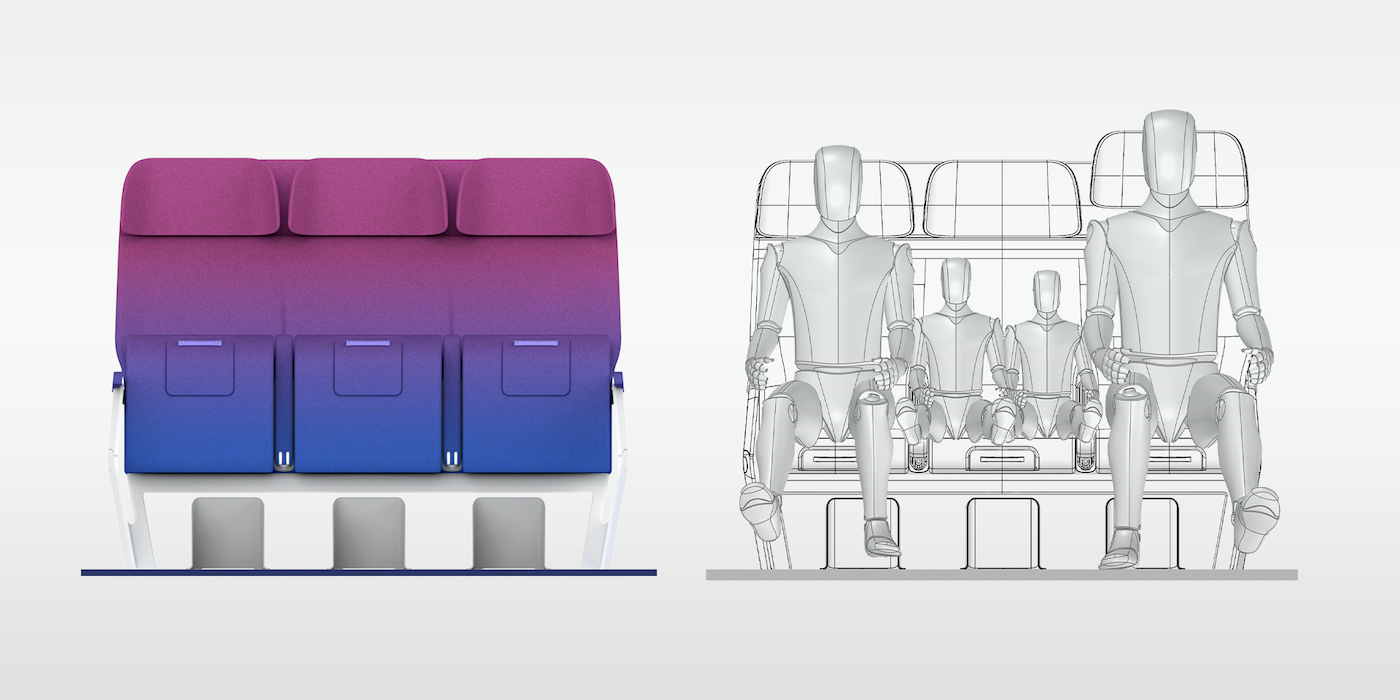
“Not only did we want to do something innovative, but also we wanted to save weight and reduce production times, while strictly respecting the parameters imposed by the aeronautical certification standards for seats, furnishings and components,” explains Matteo Bulletti, aeronautical engineer and managing director of Delta Interior Design “Especially after the pandemic, it will be very important to guarantee safety and hygiene on board aircraft. New technologies allow great margins for improvement, such as touchless toilets that avoid contact with surfaces potentially exposed to bacteria”.
From a regulations point of view, both the European Aviation Safety Agency (EASA) and the Federal Aviation Administration (FAA) require new designs to achieve ETSO/TSO certification and to demonstrate that, in the event of a crash, the seat belts support the standard passenger weight, as required by CS-FAR 25.785. The seat dimensions and the inclination of the backrest are also regulated, as well as the resistance of the seat structure, which should be able to absorb loads up to 16-times the force of gravity (16G). The project also proposes improved inflight entertainment (IFE) systems with larger and more curved displays, overhead lockers that can be opened and closed via a smartphone app, and a toilet booking system, which also works through an app.
Innovative materials
The materials used for cabin furnishing elements are typically divided into two categories: those that make up the structural parts, such as the seat frame, galleys and lavatories; and the aesthetic ‘soft product’ materials, such as fabrics and cushions.
The RATIOS programme researchers looked at both hard and soft goods, evaluating new materials, and some that are already used in other fields such as automotive and construction. In addition to considering pure innovation, the team investigated different aspects of the materials that are often not taken into consideration. For example, in addition to the traditional evaluation parameters, the team also considered whether materials had low or zero environmental impact, through being ecological, recyclable or sustainable.
The team also looked at trim and finish materials are concerned, including a focus on fabrics made with natural materials such as hemp and cotton, not sourced from any supplier that uses intensive manufacturing methods or treats materials with pesticides or fertilisers. They also appreciated efforts made to minimise the environmental impact of traditional chemical processes for the fabric dyes, also with an eye on decreased energy and water consumption, achieved by reducing the temperatures involved in the colouring process.
The research explored the possible treatments for these new materials. In order to be installed in an aircraft cabin, especially for passenger transport, all materials must demonstrate a high level of safety. In the case of non-metallic materials, such as fabrics, plastic laminates and composites, the main requirement is with regard to flammability: the materials must demonstrate a high self-extinguishing capacity, low emission of fumes, and a lack of potentially toxic elements. Treatments are available which, when applied to fabrics and leathers, allow their fire-retardant properties to be increased significantly.
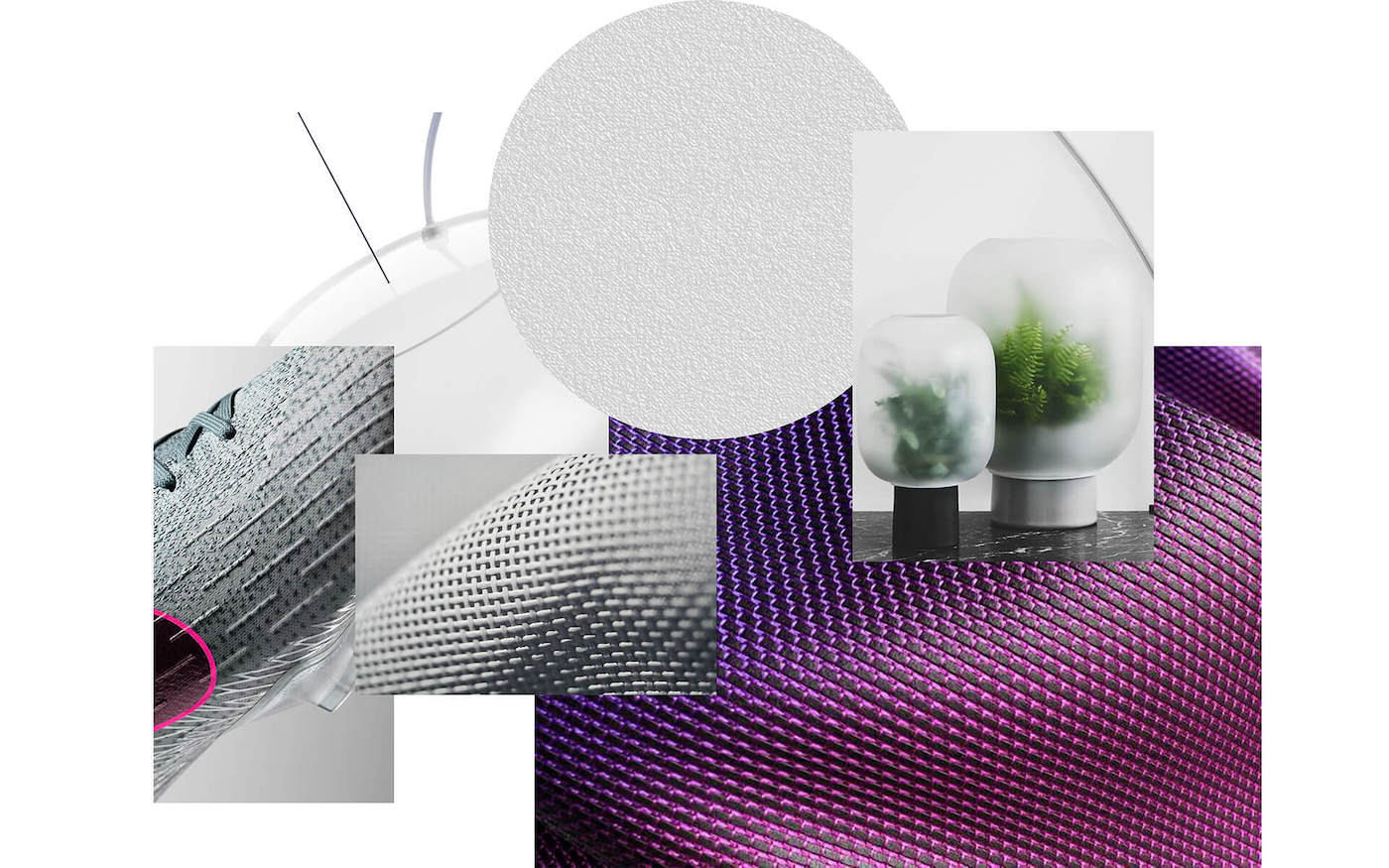
Once the new materials are tested and approved following the standard rules, they will significantly increase the range of finish options that can be installed on airplanes. There are also treatments that, using nano-technologies, can increase a material’s properties of hydro and oil-repellency, and its resistance to bacteriological and microbial contamination. These stain-proof properties can contribute to reducing the washing and sanitisation cycles of seat covers, significantly reducing the use of detergents, and thus their dispersion in the environment, as well as cutting maintenance costs for airlines.
With regard to structural materials, the research team say they have demonstrated the feasibility of using new polymers with mechanical characteristics similar to those of the alloys currently used in aircraft (such as aluminium), but with lower density. The molecular structure of the polymers studied can be modified according to needs: for example, the base polymer can be enhanced with reinforcement matrices (such as glass fibres, carbon or boron), to increase its mechanical characteristics, or it can be mixed with other elements that can significantly decrease its density, bringing significant benefits in terms of weight but with no detriment to the mechanical characteristics.
In particular, the use of microspheres (glass bubbles) mixed in appropriate percentages with polymers (nylon, polysulfone or polycarbonate, for example), can reduce the weight of a product by up to 35%, without causing any significant cost to mechanical characteristics. Note that the use of these microspheres does not require modification of the moulds in current use: on the contrary, the new mixture improves the production process. Another interesting material is a laminate created by layering unidirectional carbon fibres. The resulting sheet combines the flexibility of thermoplastics with mechanical characteristics comparable to the most common metal alloys (aluminium or magnesium). The thickness and orientation of the fibres can be designed according to the structural and dimensional needs of the foil.
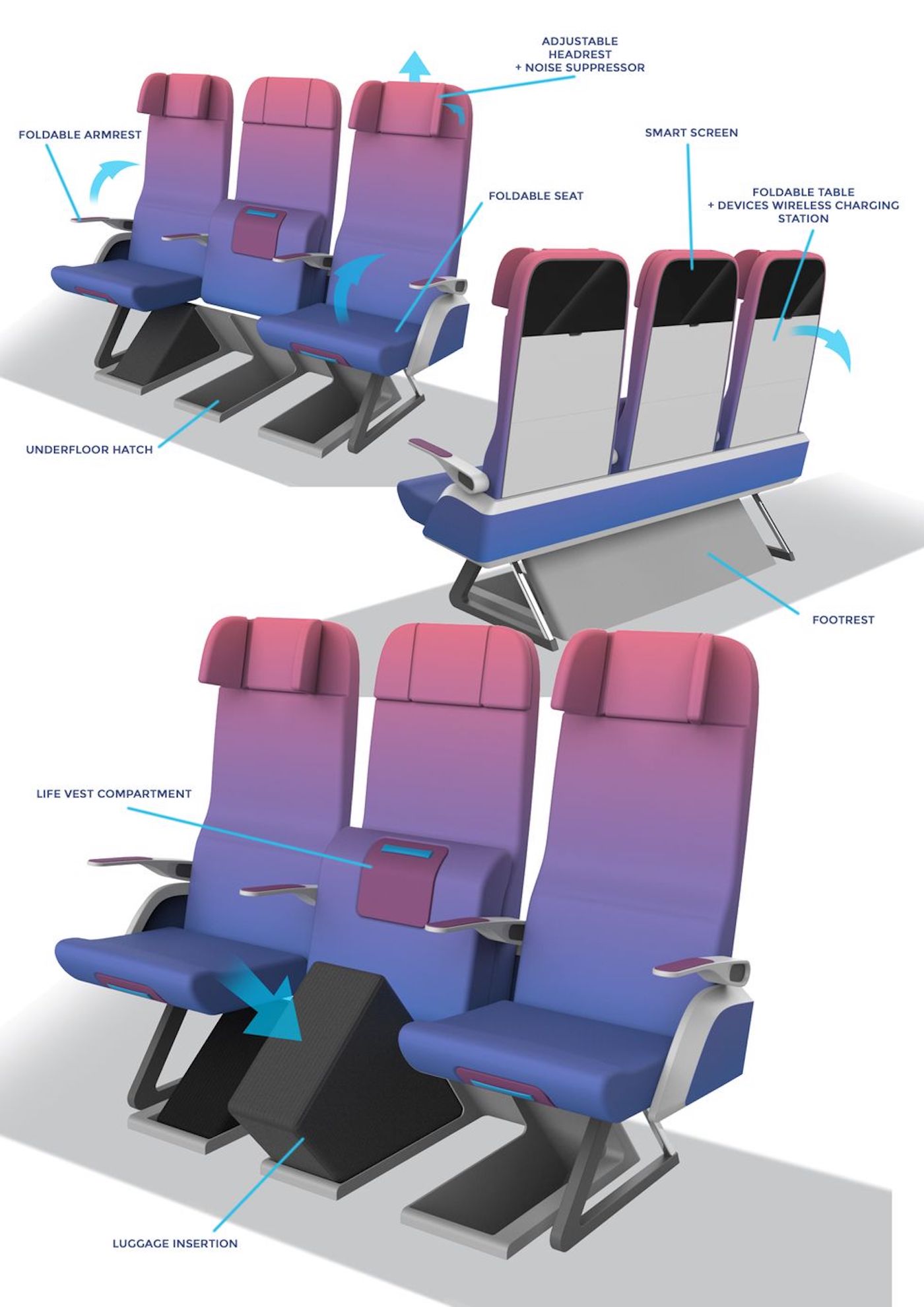
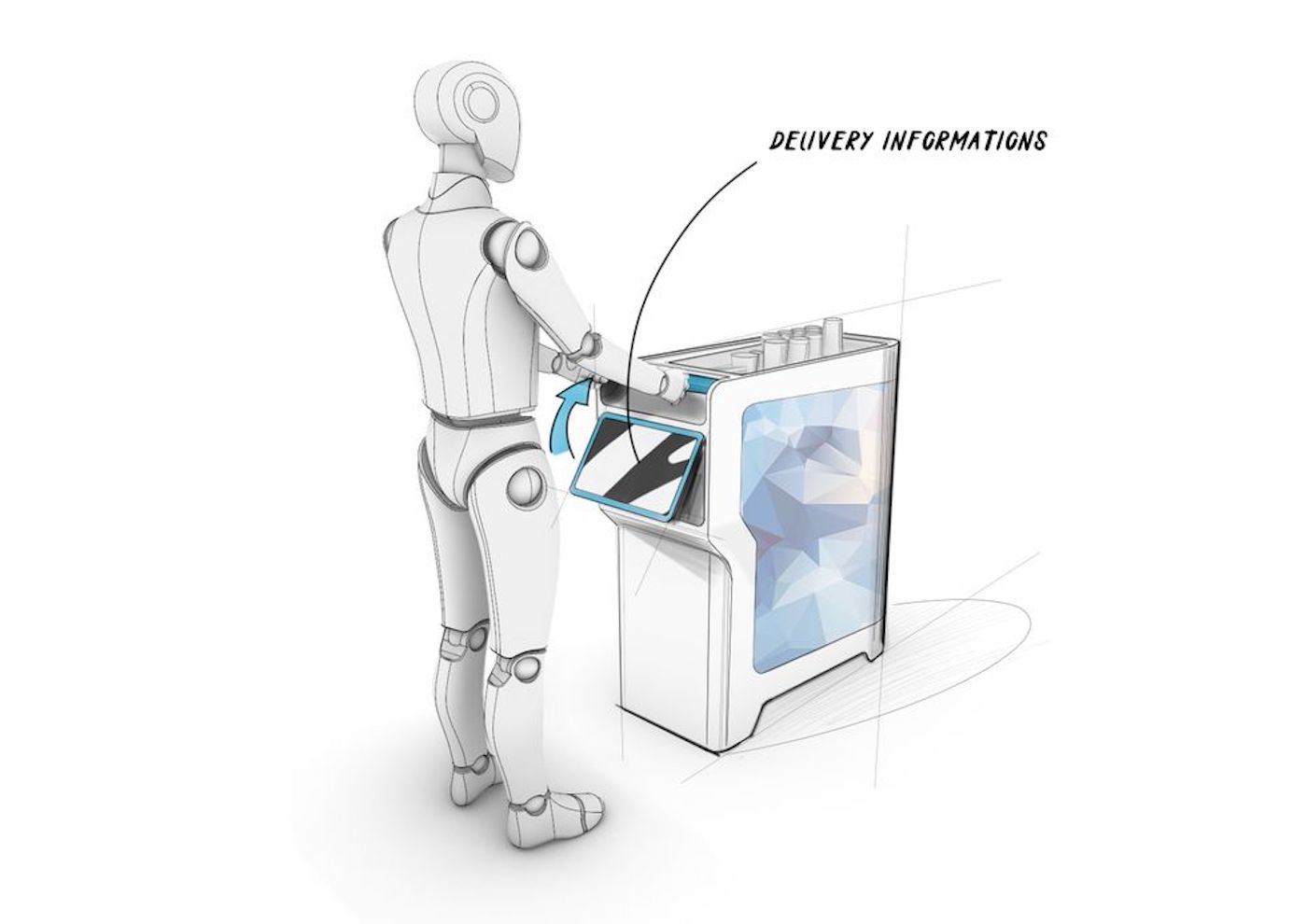
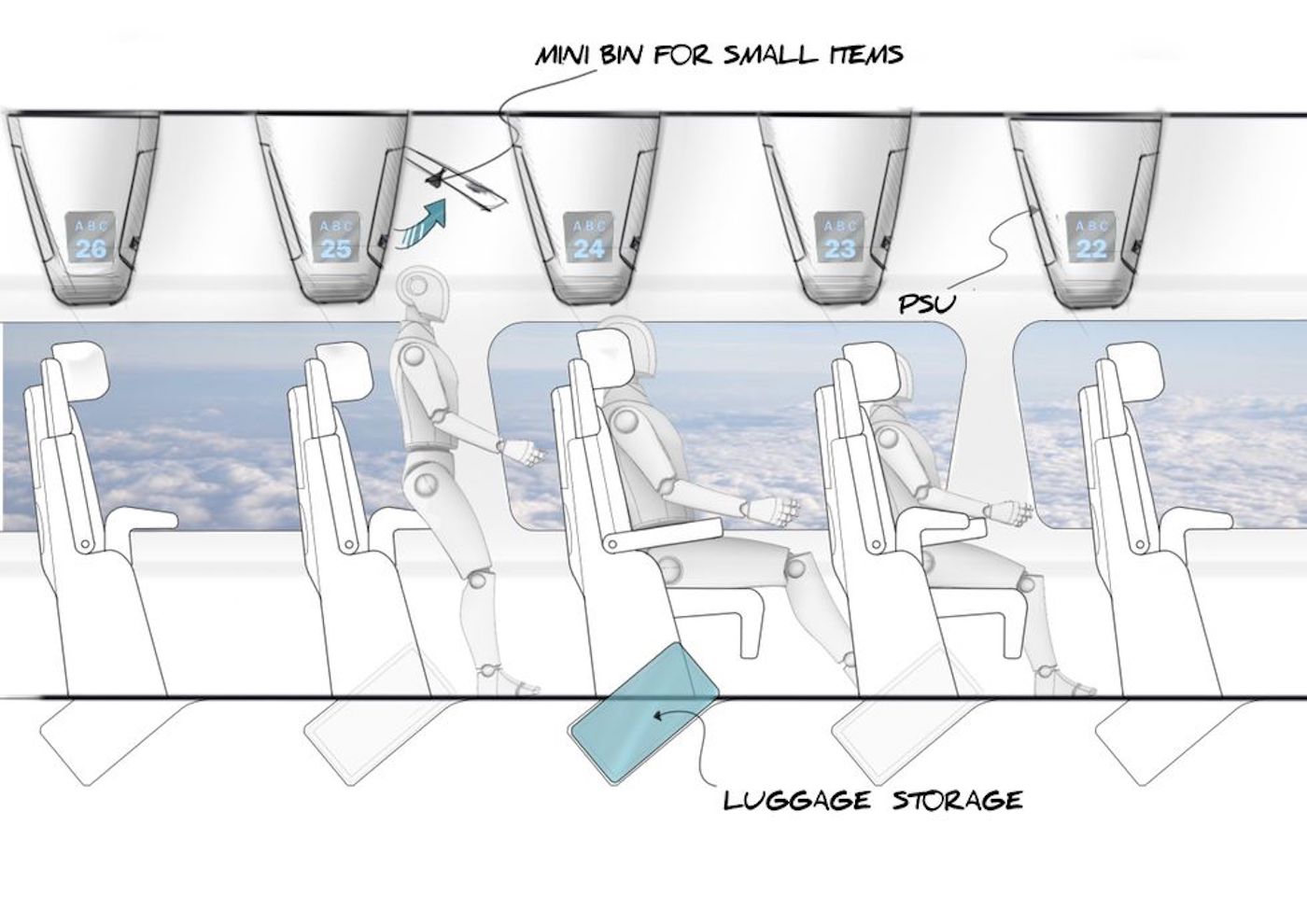