Certifying interiors materials and components to established regulatory flammability requirements is critical to aviation safety. The development of testing standards, and vigilant compliance with those standards, has undoubtedly saved lives and reduced passenger injuries in aircraft accidents.
However, the process of certification can be confusing to those trying to introduce new materials into aircraft cabin designs. If their compositions have not been previously tested, these can react in unexpected ways when exposed to flame. Test failures delay components and force a rush to find alternative materials, or to find new ways to configure combinations of materials which adequately self-extinguish and produce low heat and smoke emissions. These complications can stifle innovation, but they don’t have to.
For designers, manufacturers and airlines, success depends on striking a balance between the desire to innovate and the need to clear the hurdles of testing. By understanding the importance of the regulations, communicating effectively, collaborating on certification issues when they arise, and ensuring adherence to the letter and spirit of the laws, new programs have been realized and new materials introduced.
The CMF designers’ view
We spoke to experts who have confronted certification challenges and overcome them in different ways, without compromising safety.
Maria Kafel Bentkowska and Yod Suntanaphan are senior CMF designers at design firm PriestmanGoode, whose department takes up an entire floor of the firm’s new offices in London. These experts like to be increasingly involved in the certification processes, in order to understand the technical requirements.
As Bentkowska says, “The more you understand, the more you know, the better you can use that experience to select materials which are more likely to pass, but which also have the aesthetic properties you want to incorporate in a design program. Some are trickier than others.”
Some materials are more volatile, or more likely to produce toxic smoke emissions than others. Very few can make it into the aircraft cabin untreated. Some natural materials have inherent favourable flammability properties – sheepskin and wool, for example – but they may not meet the aesthetic needs of particular design concepts, nor fit a particular application. To ensure that many attractive materials and composites pass the tests, chemicals are used to make the materials flame-retardant, but finding the right flame retardant is a delicate process, with no guarantees. Using such chemicals also increases the risk of the aesthetics, malleability, durability and service life of a material being altered.
“There is no standard formula of getting flammability to pass,” Suntanaphan says. “The materials suppliers know how to adjust the formulas accordingly, so that any product features that affect flammability can be resolved. They are the ones making the product and they are familiar with producing materials that pass.”
Bentkowska believes the secret lies in working with suppliers from the beginning. “We work closely with the suppliers on these certifications,” she states. “It’s their business to understand precisely how the treatments and fire test properties of these materials work. We work with them to identify high-risk items as early as possible, which leaves everyone more time to find solutions in case there are complications.”
Incorporating new and innovative materials requires buy-in from all stakeholders in the project: the airline, the materials suppliers, the component manufacturers and the aircraft manufacturer. Because the manufacturers are responsible for the ultimate certification burden of the aircraft, they have a strong influence on materials selection. To avoid delays in their production line, both Airbus and Boeing encourage proven materials and components, already approved as part of the catalogue.
“The aircraft manufacturer’s classification of the materials can also influence the flammability testing process,” says Suntanaphan. “If a product is considered under its standalone properties, then that is one thing, but sometimes the certification is incorporated as part of the bulkhead or seat certificate. This affects the development time, and project timelines can sometimes be short. The process for approval of these material combinations in aviation can be lengthy.”
Composite testing
It is difficult enough to pass a new standalone material, but the complications are multiplied when running composite testing because the chemical interaction of the various elements can change the results of the tests. Even materials that pass the tests as a standalone material may not pass when combined. This failure sometimes results from the way the chemical properties of each material interact when set aflame. At other times, especially if an adhesive is required to bond the materials, the adhesive changes the flammability properties of the standalone materials, leading to test failure.
Aviation interiors consultant Vern Alg, who has 30 years of experience working in aviation, and has worked for more than 20 of those years as director of projects and senior manager of interiors engineering at Continental Airlines, agrees that adhesives can generate serious difficulties in certifying composites. “The adhesive is particularly problematic,” he says. “Nearly every time you encounter a problem with composites, it’s the adhesive.”
The chemical properties of the adhesives which have the best performance in their primary function often mean they result in test failures. To create a firm bond, those adhesives often contain volatile chemicals, and that volatility of the adhesive causes the composite material to fail. To counter this failure, the other material layers must be even more flame-retardant. However, treating the other materials with alternative flame retardants in order to better absorb the flammability properties of the adhesive can detrimentally affect other properties of the composite, such as color, durability and texture. Fixing one problem generates another.
Alg understands the frustrations of these challenges and has some advice for airlines, designers and manufacturers running the gauntlet of experimentation. He suggests starting with the right frame of mind and taking nothing for granted. “Flammability is key to safety,” Alg says. “There is no generalization on flammability. All material in the substrate must be specifically tested, and each must pass. Every vertical surface needs to be tested. If you change one element of a composite, it needs to be tested.”
The prospect of having to validate so many variables may be daunting. Creating new material combinations takes time, so the program timeline must have room built-in for a few rounds of trial and error, and increased product development costs.
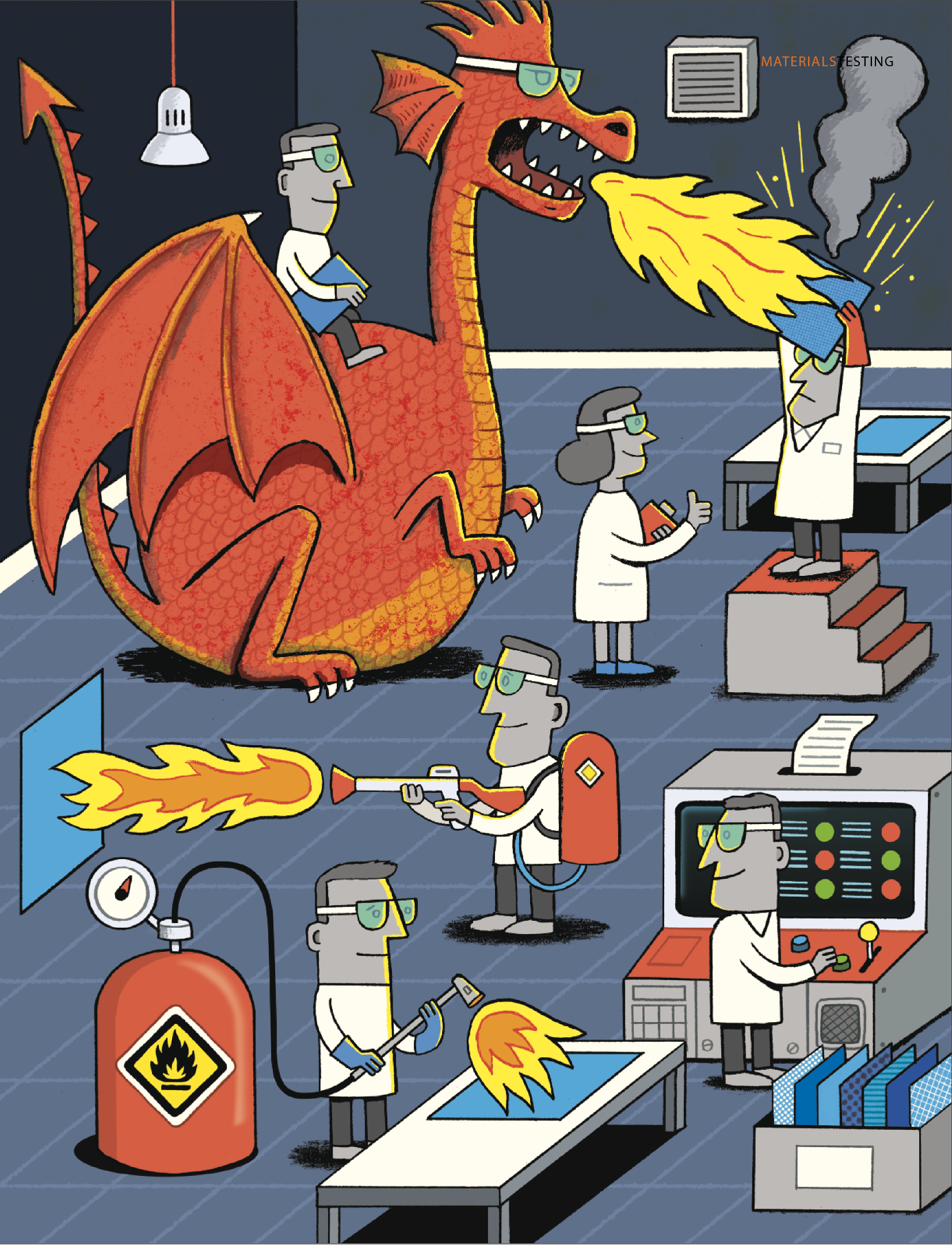
Sound advice
Alg says that the work involved in materials testing should not discourage innovation. With adequate planning up-front, and the counsel of experts, the likelihood of passing increases. “Work with good laboratories,” Alg suggests. “There are many excellent laboratories in the USA and in Europe. Work closely with your suppliers. Get the testing coupons for all the component materials, and be really up front with the FAA. There are no shortcuts.”
Alg acknowledges that some programs are difficult, but by planning ahead and verifying the compliance of individual materials and their combined effect, he suggests, the process can be smooth.
Both Bentkowska and Suntanaphan from PriestmanGoode agree with Alg that careful planning, factoring in room for rounds of trials, and good partners in the project are all essential to success.
“Combination tests are complicated because of the different requirements for each of the component materials and the different glues or adhesives used to bring them together,” says Suntanaphan. “Materials might be certified on their own, but when combined, it can go really wrong. The suppliers we work with specialize in resolving these issues when they arise.”
Should an issue be particularly troublesome, Suntanaphan has a plan in place: “We always maintain fall-back options for programs, in case there is a problem with a particular material passing.”
Supplier view
Kevin O’Brien, director of operations at Tapis Corporation, an aviation textiles supplier, has first-hand experience of just how complex composite flammability tests can be, and what can go wrong. According to O’Brien, failures lead to innovation, which can have long-term benefits, such as expanding the company’s palette for aircraft interiors, and generating new materials that address the most baffling problems.
“The biggest challenge we had a couple of years ago with our Ultraleather product was that vertical surfaces are required to meet OSU Heat Release,” he says. “In the past, we only flame-treated our materials through a post-manufacturing secondary FR process, which presented many challenges when our product was used in various composite build-ups. We’ve since developed new manufacturing procedures that incorporate the flame retardants right into the manufacturing process. It’s made the material very flame-resistant and stable.
“This new specification has also made it possible to incorporate Ultraleather into composite combinations: on thermoplastics and honeycomb composites, for example. The customer can now use their adhesive of choice, without dependency on water-based adhesives.”
The test O’Brien refers to is FAR 65/65, which governs vertical surfaces and has stringent heat-emissions and smoke-emissions limits. “FAR 65/65 specifications may not work for all combinations of materials,” he says. “If the product did not go through the proper treatments for FAR 65/65, then it limits the combinations it can be used for. We can treat the baseline product appropriately so that the 65/65 passes, in the combination of materials intended, with fewer limitations.
This new material specification resulted from solving a common problem, and, according to Tapis, it represents an important step forward for materials flammability options. However, it would never have happened without the willingness of others to try something different, and to stick with the program through the flammability challenges until a solution was found. Test failures can be a catalyst for innovation, rather than the end of it.
A new world of certification
Alg points out that the aircraft interiors industry has made great progress in this area, and that a number of new materials, adhesives and processes have emerged that make certifying easier today. “It’s a whole different world,” he says. “We’ve really come a long way.”
O’Brien agrees with Alg on the level of progress in the industry, but he also points out there is still much work to do – especially on the standards for the tests themselves. “One challenge still to overcome is that the test is imperfect,” O’Brien says, referring to the OSU Test for FAR 65/65. “There are great variances from laboratory to laboratory. The testing variability between facilities is a problem.”
Few know flammability testing better than Tim Marker of the FAA’s William J Hughes Technical Center, located just outside Atlantic City. Marker spends his days at the world’s premier flammability laboratories, testing materials no one has ever used and developing new tests when no established tests are available. He creates experiments to develop the standards, in order to ensure that aircraft safety remains assured and that new developments can find their way into the aircraft cabin. Marker is working on a new project, still in the development phase, which will ultimately improve the OSU testing issue that O’Brien raises.
“The HR2 Flammability test work we are doing is a research project,” Marker emphasizes. There are still many steps to take before the research is completed, and more trial and error to go through before the test protocols can be defined and standardized, but his efforts will yield improved FAR 65/65 testing.
“HR2 is a newer OSU apparatus, a modified version of the test which will ultimately reduce inter-lab variability. We’re trying to make the tests more repeatable. The International Materials Fire Test Working Groups can benefit from the new methodologies. There would ultimately be bilateral adoption. The regulatory effort we currently have in place is about doing research. The NCRM would come out in stages, once we have completed our research.”
Fire safety working groups
Developing the new OSU test for FAR 65/65 is not the only item on the agenda for Marker and the FAA team at Hughes.
“We have a general regulatory effort to put together a new flammability workbook, which puts all flammability questions under one roof,” Marker states. Such a book would make finding the right regulation for different applications an easier process, and also make the flammability process easier on the whole for stakeholders to understand and manage. “When that book is implemented, we will also pass along advisory language, which discusses the various processes of flammability,” Marker says.
Even as these projects are underway, industry representatives can gain important insights into flammability through participation in the open Fire Safety Working Group meetings.
Marker gives us one more bit of good news, which could help innovators better predict the results of new testing combinations. “There is work on the industry side to develop a catalogue of products,” he says. “QA arrangements could be made with the certification office to reduce the steps for approval of virgin products.”
But Marker also reminds us why these regulations and tests are vital for aviation, and how much importance we must place on ensuring that we respect and adhere to the requirements. “All the flammability tests are based on full-scale testing at the Hughes Technical Center lab. None of them are arbitrary. They come as a result of the insights we gain from intensive testing, which reveals the safety risks of various materials. The intent is to reduce fatalities.”
As Bentkowska says: “The safety of aircraft is the priority. Everyone has a role to play in ensuring that.”