In an era when consumer expectations are sky-high, the aerospace industry faces the constant challenge of revitalising older aircraft to meet modern standards. Imagine stepping onto a 20-year-old aircraft and being greeted by an environment that feels entirely contemporary, complete with state-of-the-art digital displays, plush seating, and a welcoming entryway. This transformative experience is made possible through the meticulous process of aircraft modification, where engineering ingenuity meets visionary design.
The need for innovation

Aircraft modifications extend far beyond the mere replacement of old interiors with new ones; they entail comprehensive enhancements that affect every aspect of the cabin. This process involves crafting an environment that not only aligns with an airline’s brand identity, but also surpasses passenger expectations in terms of comfort and functionality. Such modifications can transform the passenger experience by introducing state-of-the-art amenities, ergonomic seating, and aesthetic improvements that together create a harmonious and inviting atmosphere.
One of the primary challenges in this area arises from the constraints of the production systems used by original equipment manufacturers (OEMs). Typically designed for uniformity and mass-production efficiency, these systems often lack the flexibility required for the custom innovations that airlines increasingly desire to differentiate their service.
Here, companies like Jamco America, an experienced turnkey aircraft interior integrator, play a critical role by providing the flexibility and specialist expertise that OEMs cannot. By collaborating with airlines, modification experts can realise bespoke visions, transforming ideas into certified and airworthy designs. This level of customisation not only meets the specific needs and wants of airlines, but also enhances the overall value and appeal of the aircraft.
Collaborative innovation in design
A key aspect of successful aircraft modification is early collaboration between modification companies and airlines. By engaging at the ideation stage, both parties can explore and prototype innovative layouts and features that push conventional limits while being feasible and aligned with the airline’s aspirations.
The surge in market demand, particularly post-Covid-19, underscores the urgency for upgrades. Airlines, recognising the potential to revitalise their customer base, are investing in modifications that promise enhanced travel experiences. Upgrades such as state-of-the-art entrance areas that maintain brand continuity from lounge to aircraft are becoming increasingly popular.
Enhancing functionality and experience
In the competitive field of aircraft interiors, it’s not just about making visual upgrades. Functionality plays a critical role, with technological enhancements such as better connectivity, larger and higher-resolution screens, and intuitive user interfaces becoming standard expectations.
Space optimisation is another critical area. Innovative seating layouts and strategically placed partitions can increase capacity while preserving or enhancing comfort. Increasing passenger count without diminishing the travel experience is now achievable through innovative aircraft interior solutions.
Seating products are designed to maximise space efficiency, integrating seamlessly with other cabin elements such as lavatories and overhead bins, which are larger and rarely run out of space. Innovative dividers also play a dual role; they serve as partitions while providing additional space beneath for passengers’s feet or luggage. This intelligent design allows for more seats to be added without compromising comfort or convenience for passengers.
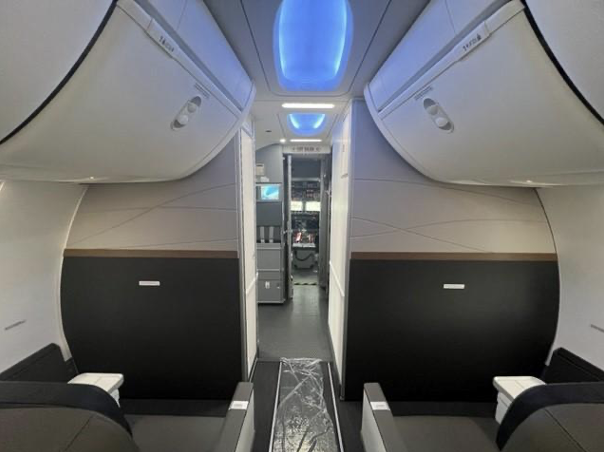
Sustainable and efficient design
Sustainability is becoming a cornerstone of modern aircraft design. Lighter, more environmentally friendly materials are being employed not only to reduce the aircraft’s weight and thus its fuel consumption, but also to minimise the ecological footprint of manufacturing and operational processes.
For example, Jamco is advancing aircraft interior technologies by exploring and implementing new, more sustainable materials aimed at reducing aircraft weight and enhancing efficiency. Among these innovations is HX5 from Alpine, a revolutionary nanocomposite that has the strength of aluminium at just half the weight. Crafted for the aerospace sector, HX5 marks a significant stride toward lighter aircraft.
Jamco’s R&D team is also developing a new lightweight floor panel material, designed to meet essential structural and safety standards while also reducing overall weight, supporting the aviation industry’s push toward sustainability and efficiency.
Integration and collaboration
As the aerospace industry evolves towards interiors that rival the personalised, high-quality environments seen in the automotive industry, the role of specialised aircraft modification companies becomes increasingly vital. These companies not only understand the technical requirements, but also appreciate the aesthetic and functional aspirations of airlines and their passengers.
With a commitment to innovation, sustainability, and passenger satisfaction, the future of aircraft interiors looks promising, offering experiences that are both enjoyable and in tune with contemporary expectations. The collaboration between integrators and their airline partners is key to navigating this complex but exciting landscape.
Adopting a cohesive and integrated approach to designing aircraft interiors, including stowage systems, seating, galleys, and lavatories, ensures that all components work harmoniously both in function and design, creating a unified aesthetic. Moreover, partnering with an experienced integrator will not only facilitate this seamless integration, but also ensure the smooth execution of installation or retrofit processes, staying within budget and schedule constraints. This comprehensive strategy is preferable to engaging multiple vendors for disparate components.