Senior Aerospace BWT, a UK-based manufacturer of low-pressure air ducting and air handling systems for aerospace, has grown its production capacity with the installation of 3D printers for the additive manufacturing of thermoplastic aircraft interior parts.
The company’s site in Macclesfield is now equipped with two industrial-grade Stratasys Fortus 450mc 3D printers, which will use aerospace-grade Ultem 9085 resin, following a testing and qualification programme to ensure its suitability for use in aircraft interior components.
Darren Butterworth, CEO, Senior Aerospace BWT, commented, “After two years of intensive R&D work, we have qualified the associated products and processes, which enable us to produce flight-ready parts quickly and cost-effectively for our customers. We now have the capability of deploying a robust, accurate, repeatable and traceable process – which is what the industry demands.”
The company states that the 3D printing technologies yield “significant savings” in terms of component weight, cost and lead-time, compared with the use of aluminium. For certain parts, Senior Aerospace BWT claims savings of as much as 75% – particularly for small order quantities.
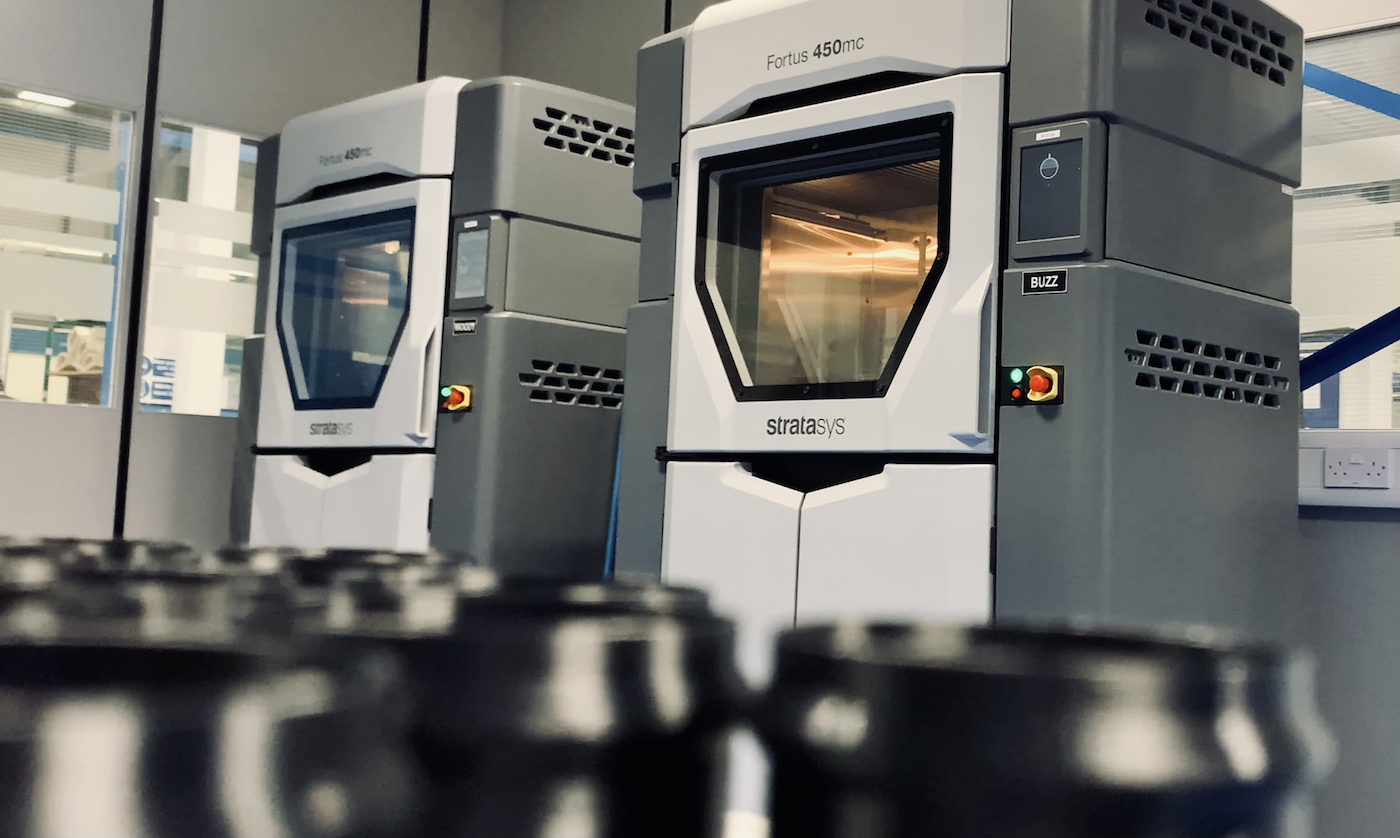
“In many cases, minimum order quantities for off-the-shelf aluminium parts make traditional manufacturing simply unviable when we may only need a handful for one aircraft,” added Butterworth. “If you add to that the small, complex geometries of some parts, it just does not warrant the cost and time to CNC machine them in aluminium.”
Senior Aerospace BWT first began investigating the commercial viability of FDM 3D printing for interior aircraft parts over four years ago via a technical partnership with a service bureau. Through the collaboration, the company delivered its first duct incorporating a 3D-printed part for flight use on regional passenger jets in 2018. Since then, the company has supplied customers with hundreds of lightweight, flight-ready interior aircraft parts using FDM, often incorporating highly complex geometries.